Development of geopolymer mortar made from bagasse ash with waste aluminum
DOI:
https://doi.org/10.55674/cs.v16i2.254773Keywords:
Bagasse ash, Aluminum scrap, Geopolymer Mortar, Compressive strength, Waste materialsAbstract
Geopolymer concrete is a type of concrete that is produced using industrial waste materials such as fly ash, slag, and other similar materials instead of traditional Portland cement. This research studied the variables affecting geopolymer mortar from bagasse ash mixed with aluminum scraps. The waste materials, bagasse ash (BA) and aluminium scrap (AL) were crushed to reduce the particles by grinding. An amount of ALU 0.01 – 0.15 wt% bagasse (BA) ash was added to the mixture. The alkaline solutions (AS) used to leach silicon oxide and aluminium oxide from BA were sodium hydroxide (NH) and sodium silicate (NS). The concentration of NH solution was varied between 7.5 – 15 molar. The ratio of alkaline solution to bagasse ash (AS/BA) was controlled at 0.50. Mortar samples were cast and cured at 60 80 and 100 °C for 48 hours. The results showed that the 10-molar sodium hydroxide solution tended to support the higher compressive strength. The highest compressive strength of geopolymer was found when using 0.04% aluminum scrap and curing at 80 °C. The additional water improved the workability of the fresh mortar, but the lower strength of the geopolymers was archived.
GRAPHICAL ABSTRACT
HIGHLIGHTS
- Do not use as a cementitious binder
- Reuse waste materials
- It is an environmentally friendly and sustainable material
References
L. Poudyal, A. Kushal, Environmental sustainability in cement industry: An integrated approach for green and economical cement production, Resour. Environ. Sustainability. 4 (2021) 100024.
TCMA Annual Report 2019, https://www.thaicma.or.th/th/ebook_detail/1/147, 27 October 2022.
F. Batool, A. Masood, M. Ali, Characterization of sugarcane bagasse ash as pozzolan and influence on concrete properties, Arabian J. Sci. Eng. 45 (2020) 3891 – 3900.
A. Tripathy, P.K. Acharya, Characterization of bagasse ash and its sustainable use in concrete as a supplementary binder–A review, Constr. Build. Mater. 322 (2022) 126391.
American Society for Testing and Materials (ASTM), Standard specification for coal fly ash and raw or calcined natural pozzolan for use in concrete. Release, C-618 Specification, 2012.
S.R. Teixeira, A.E.D. Souza, G.T.D.A. Santos, A.F.V. Peña, Á.G. Miguel, Sugar cane bagasse ash as a potential quartz replacement in red ceramic, J. Am. Ceram. Soc. 91(6) (2008) 1883 – 1887.
G.C. Cordeiro, K.E. Kurtis, Effect of mechanical processing on sugar cane bagasse ash pozzolanicity, Cem. Concr. Res. 97 (2017) 41 – 49.
Industrialclub, Aluminium Industry Club, https://industrial club.fti.or.th/2022/02/21, 28 October 2022.
S. Onutai, S. Jiemsirilers, P. Thavorniti, T. Kobayashi, Aluminium hydroxide waste based geopolymer composed of fly ash for sustainable cement materials, Constr. Build. Mater. 101 (2015) 298 – 308.
J. Davidovits, Geopolymers and geopolymeric materials, J. Therm. Anal. 35 (1989) 429 – 441.
J. Davidovits, Properties of geopolymer cements, The 1st international conference on alkaline cements and concretes, Scientific research institute on binders and materials, Kiev State Technical University. October 1994, 131 – 149.
S. Puttala, W. Hiranphattararoj, S. Homwuttiwong, Development of a geopolymer made from bagasse ash for use as a cementitious material, APST. Journal. 26(4) (2021) 1 – 10.
American Society for Testing and Materials (ASTM), Standard practice for making and curing concrete test specimens in the laboratory. Release, C192/C192M-16a Laboratory, 2016.
American Society for Testing and Materials (ASTM), Standard Test Method for Compressive Strength of Hydraulic Cement Mortars (Using 2-in. or [50-mm] Cube Specimens), C109/C109M-20, 2020.
J. Wongpa, K. Kiattikomol, C. Jaturapitakkul, P. Chidaprasirt, Compressive strength, modulus of elasticity, and water permeability of inorganic polymer concrete, Mater. Des. 31(10) (2010) 4748 – 4754.
Z. Zuhua, Y. Xiao, Z. Huajun, C. Yue, Role of water in the synthesis of calcined kaolin-based geopolymer, Appl. Clay. Sci. 43(2) (2009) 218 – 23.
S. Puttala, S. Homwutiwong, The effect of the solution on compressive strength of geopolymer concrete bagasse ash, The 24th national convention on civil engineering, Udonthani. 10 – 12 July 2019, 761 – 765.
A. Hassan, M. Arif, M. Shariq, Age‐dependent compressive strength and elastic modulus of fly ash‐based geopolymer concrete, Struct. Concr. 23(1) (2022) 473 – 487.
C.D. Atiş, E.B. Görür, O. Karahan, C. Bilim, S. İlkentapar, E. Luga, Very high strength (120MPa) class F fly ash geopolymer mortar activated at different NaOH amount, heat curing temperature and heat curing duration, Constr. Build. Mater. 96 (2015) 673 – 678.
J.J. Ekaputri, S. Junaedi, Wijaya, Effect of curing temperature and fiber on metakaolin-based geopolymer, Procedia. Eng. 171 (2017): 572 – 583.
C. Tippayasam, P. Balyore, P. Thavorniti, E. Kamseu, C. Leonelli, P. Chindaprasirt, D. Chaysuwan, Potassium alkali concentration and heat treatment affected metakaolin-based geopolymer, Constr. Build. Mat. 104 (2016) 293 – 297.
P. Sajan, T. Jiang, C.K. Lau, G. Tan, K. Ng, Combined effect of curing temperature, curing period and alkaline concentration on the mechanical properties of fly ash-based geopolymer, Clean. Mater. 1 (2021) 100002.
M. Muracchioli, G. Menardi, M.D. Agostini, G. Franchin, P. Colombo, Modeling the compressive strength of metakaolin-based geopolymers based on the statistical analysis of experimental data, Appl. Clay. Sci. 242 (2023) 107020.
K. Sagoe-Crentsil, L. Weng, Dissolution processes, hydrolysis and condensation reactions during geopolymer synthesis: Part II. High Si/Al ratio systems. J. Mater. Sci. 42(2007) 3007 – 3014.
J. Archez, A. Gharzouni, I. Sobrados, A. Piancastelli, J.F. Caron, N. Texier-Mandoki, X. Bourbon, S. Rossignol, Geopolymer local network evolution under time and temperature, J. Non. Cryst. Solids. 566 (2021) 120870.
J.G.S. van Jaarsveld, J.S.J. van Deventer, G.C. Lukey, The effect of composition and temperature on the properties of fly ash-and kaolinite-based geopolymers, Chem. Eng. J. 89(1 – 3) (2002) 63 – 73.
X. Ma, Z. Zhang, A. Wang, The transition of fly ash-based geopolymer gels into ordered structures and the effect on the compressive strength, Constr. Build. Mater. 104 (2016) 25 – 33.
M.G. Khalil, F. Elgabbas, MS. El-Feky, H. El-Shafie, Performance of geopolymer mortar cured under ambient temperature, Constr. Build. Mater. 242 (2020) 118090.
N. Zhang, A. Hedayat, L. Figueroa, K.X. Steirer, L. Li, H.G.B. Sosa, Physical, mechanical, cracking, and damage properties of mine tailings-based geopolymer: Experimental and numerical investigations, J. Build. Eng. 75(2023) 107075.
C.Y. Heah, H. Kamarudin, A.M. Mustafa Al Bakri, M. Bnhussain, M. Luqman, I. Khairul Nizar, C.M. Ruzaidi & Y.M. Liew, Kaolin-based geopolymers with various NaOH concentrations, Int. J. Miner. Metall. 20(3) (2013) 313 – 322.
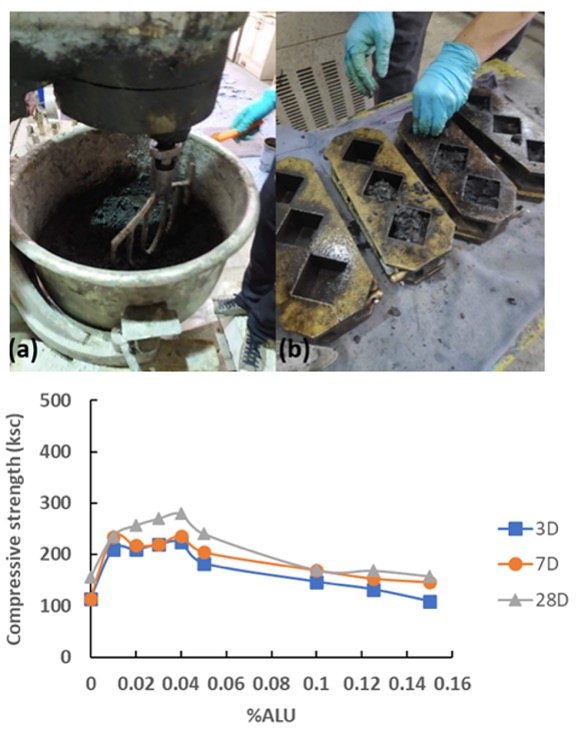
Downloads
Published
How to Cite
Issue
Section
Categories
License
Copyright (c) 2024 Creative Science

This work is licensed under a Creative Commons Attribution-NonCommercial-NoDerivatives 4.0 International License.