Physical and Mechanical Properties of Natural Rubber Composites Filled with Rice Husk and Rice Straw
Keywords:
natural rubber composite, natural latex, rice straw, rice husk, bio compositeAbstract
In this work, the natural rubber (NR) composites filled with two wastes from rice cultivation, such as rice husk (RH) and rice straw (RS) were studied. Different sizes of each waste were prepared which were RH-S, RH-L, RS-S, and RS-L and used as fillers in composites. The effects of filler types and contents (15, 30 and 45 phr) on the physical and mechanical properties of NR composites were studied. The results showed that NR composites reinforced with RS and RH had lower densities than that of neat NR. The types, sizes, and contents of fillers showed minor effects on the composite’s density. Interestingly, due to the difference in the chemical composition of RS and RH, the trend of water absorption and an oil absorption of NR composites filled with RSs and RHs were different. RSs/NR composites showed a higher percentage of water absorption but RHs/NR systems showed higher oil uptake. Using larger size of fillers (RS-L and RH-L) in composites displayed higher tendency of both water and oil absorptions than that using smaller fillers. The percentage of water absorption of all types of composites was higher than that of NR sheet. This value increased with increasing filler content. In contrast, the addition of filler loading resulted in decreasing the percentage of oil absorption of all types of composites. Comparing with neat NR, Young’s moduli of all types of composite were found improved with an increase of filler loading. All RSs/NR composites were dramatically higher in effectiveness. However, a decrement of tensile strength of all composites was observed. SEM micrographs clearly revealed the lack of interfacial interaction between fillers and NR that showed the gap and hole. These evidences supported the composite properties that mentioned above.
References
[2] E. Hesammi, A. B. Talebi, A. Hesammi, A Review on the Burning of Crop Residue on the Soil Properties, WALIA. 30(1)(2014) 192–194.
[3] A. K. Mohanty, M. Misra, L. T. Drzal, Sustainable Bio-Composites from Renewable Resources: Opportunities and Challenges in the Green Materials World, J. Polym. Environ. 10 (2002) 19–26.
[4] R. P. Babu, K. O'Connor, R. Seeram, Current Progress on Bio-Based Polymers and their Future Trends, Prog. Biomater. 2(8)(2013) 1–16.
[5] A. K. Mohanty, S. Vivekanandhan, J. M. Pin, M. Misra, Composites from Renewable and Sustainable Resources: Challenges and Innovations, Science. 362(6414)(2018) 536–542.
[6] Thailand: World’s biggest rice exporter, https://millermagazine.com/english/thailand-worlds-biggest-rice- exporter/.html#:~:text=For%20most%20of%20the%20past,a%20quarter%20of%20global%20trade, 1 February 2021.
[7] S. K. Ramamoorthy, M. Skrifvars, A. Persson, A Review of Natural Fibers Used in Biocomposites: Plant, Animal and Regenerated Cellulose Fibers, Polym. Rev. 55(1)(2015) 107–162.
[8] R. Khandanlou, G. C. Ngoh,, W. T. Chong, Feasibility Study and Structural Analysis of Cellulose Isolated from Rice Husk: Microwave Irradiation, Optimization, and Treatment Process Scheme, Bioresources. 1(3)(2016) 5751–5766.
[9] M. Megahed, S. S. Ali-Eldin, S. M. M. A. E. Moezz, W. S. Abdalla, Synthesis of Developed Rice Straw Sheets and Glass Fiber-Reinforced Polyester Composites, J. Compos. Mater. 54(23)(2020) 3381–3394.
[10] S. M. L. R. Rosaa, E. F. Santosb, C. A. Ferreiraa, S. M. B. Nachtigallb, Studies on the Properties of Rice-Husk-Filled-PP Composites – Effect of Maleated PP, Mater. Res. 12(3)(2009) 333–338.
[11] R. Khandanlou, M. B. Ahmad, K. Shameli, M. Z. Hussein, N. Zainuddin, K. Kalantari, Mechanical and Thermal Stability Properties of Modified Rice Straw Fiber Blend with Polycaprolactone Composite, J. Nanomater. 2014(2014) Article ID 675258 1–10.
[12] O. S. Dahham, N. Z. Noriman, S. T. Sam, N. M. Al-Samarrai, Z. Shayfull, A. M. Alakrach, S. A. Elnaid, The Influence of Rice Husk Fibres on the Properties of Epoxidized Natural Rubber/Rice Husk Fibres Compounds, MATEC Web of Conferences. 78(01075)(2016) doi: 10.1051/matecconf/20167801075.
[13] J. Y. Tong, N. R. R. Royan, C. Ng, M. H. A. Ghani, S. Ahmad, Study of the Mechanical and Morphology Properties of Recycled HDPE Composite Using Rice Husk Filler, Adv. Mater. Sci. Eng. 2014(2014) 1–6.
[14] M. Bassyouni, S. Waheed Ul Hasan, 2015, “The Use of Rice Straw and Husk Fibers as Reinforcements in Composites, in: O. Faruk, M. Sain (Eds.), Biofiber Reinforcements in Composite Materials, Woodhead Publishing, UK, 2015, pp. 385–422.
[15] South East Asia Rubber Market Analysis and Forecasts to 2023, https://www.globenewswire.com/news-release/2020/11/09/2122683/0/en/South-East-Asia-Rubber-Market-Analysis-and-Forecasts-to-2023.html#:~:text=Asia%20accounts %20for%2093%25%20of,stood%20at%2013.804%20million%20tonnes, 1 February 2021.
[16] The Making of Latex ACE Products & Consulting, https://www.aceprodcon.com/ what-is-latex-made- of/#:~:text=Latex%20Applications&text=Natural%20rubber%20latex%20is%20most,in%20coatings%2C%20like%20latex%20paint. , 1 February 2021.
[17] H. K. Goering, P. J. V Soest, Forage fiber analyses (apparatus, reagents, procedures, and some applications) U.S. Agricultural Research Service. (1970) 1–24.
[18] S. Mirmohamadsadeghi, K. Karimi, Chapter 21 - Recovery of silica from rice straw and husk, in: S. Varjani, A. Pandey, E. Gnansounou, S. K. Khanal, S. Raveendran (Eds.), Current Developments in Biotechnology and Bioengineering, Elsevier, Netherlands, 2020, pp. 411–433.
[19] X. Li, L. G. Tabil, S. Panigrahi, Chemical Treatments of Natural Fiber for Use in Natural Fiber-Reinforced Composites: A Review, J. Polym. Environ. 15(2007) 25–33.
[20] M. Reowdecha, C. Sukthaworn, P. Dittanet, N. Moonprasith, T. Na Lampang, S. Loykulnant, P. Prapainainar, Degradation of Silica-Reinforced Natural Rubber by UV Radiation and Humidity in Soil, Key Eng. Mater. 751 (2017) 314–319.
[21] B.S. Ndazi, C. Nyahumw, J. Tesha, Chemical and Thermal Stability of Rice Husks against Alkali Treatment, BioResources. 3(4)(2007) 1267–1277.
[22] T. Sebio-Punal, S. Naya, J. Lopez-Beceiro, J. Tarrıo-Saavedra, R. Artiaga, Thermogravimetric Analysis of Wood, Holocellulose, and Lignin from Five Wood Species, J. Therm. Anal. Calorim. 109(2012) 1163–1167.
[23] A. Patnaik, A. Satapathy, S. S. Mahapatra, R. R. Dash, A Comparative Study on Different Ceramic Fillers Affecting Mechanical Properties of Glass–Polyester Composites, J. Reinf. Plast. Compos. 28(2009) 1305–1318.
[24] S. Wang, J. Liu, Y. Wu, Y. You, J. He, L. Zhang, L. Zhang, Y. Dong, Micromorphological characterization and label-fre quantitation of small rubber particle protein in natural rubber latex, Anal. Bioche. 499(2016) 39–42.
[25] P. Pornprasit, T. Rattanaplome, Composites from Biomass Using Natural Rubber Latex as a Binder, RMUTI Journal. 1(2015) 458–463.
[26] L. P. I. Jayathilaka, T. U. Ariyadasa, S. M. Egodage, Development of biodegradable natural rubber latex composites by employing corn derivative bio-fillers, J Appl Polym Sci. e49205(2020), https://doi.org/10.1002/app.49205.
[27] Y. Yang, H. Yi, C. Wang, Oil Absorbents Based on Melamine/Lignin by a Dip Adsorbing Method, Chem. Eng. 3(2015) 3012−3018.
[28] C. Piao, L. E. Winandy, T. F. Shupe, From Hydrophilicity to Hydrophobicity: A Critical Review: Part I. Wettability and Surface Behavior, Wood. Fiber. Sci. 42(4)(2010) 490–510.
[29] L. Srisuwan, K. Jarukumjorn, and N. Suppakarn, Physical Properties of Rice Husk Fibres /Natural Rubber Composites, Adv. Mat. Res. 410(2012) 90–93.
[30] J. A. Fiorote, A. P. Freire, D. S. Rodrigues, M. A. Martins, L. Andreani, L. F. Valadares, Preparation of Composites from Natural Rubber and Oil Palm Empty Fruit Bunch Cellulose: Effect of Cellulose Morphology on Properties, Bioresources. 14(2)(2019) 3168–3181.
[31] M. Masłowski, J. Miedzianowska, K. Strzelec, Natural Rubber Biocomposites Containing Corn, Barley and Wheat Straw, Polym. Test. 63(2017) 84–91.
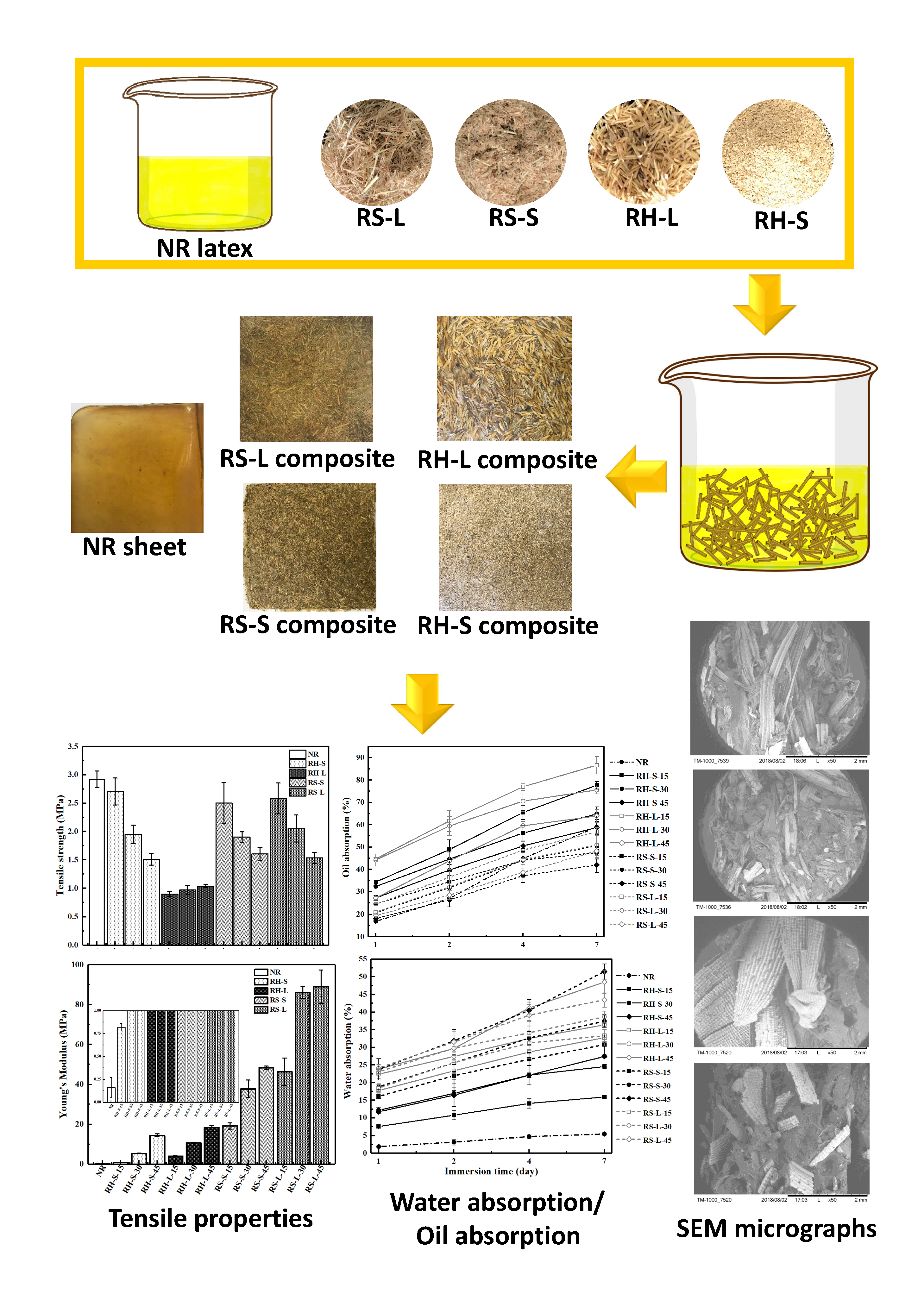