Solid fuel processing of Refuse Derived Fuel (RDF) from agricultural waste with latex rubber binder.
DOI:
https://doi.org/10.55674/cs.v17i1.258001Keywords:
Refuse Derived Fuel (RDF), Agricultural Waste, Latex RubberAbstract
There are 5 types of waste materials making up RDF: rubber wood chips (RWC), wood residues (WR), mixed grass (MG), cassava rhizome (CR), leaf fragments (LF). The heating values range 14,693-17,065 kJ/kg. The energy values range 3,509.36-4,075.91 kcal/kg. The moistures range 10.35-16.80 %. The densities range 310-550 kg/m3. Regarding physical and chemical properties of the RDF, Tested with 2 binders: cassava starch sludge and latex rubber with the ratio of 0.50:0.50. The results showed that the moistures range 7.56-8.32 by wt. %. The energy values range 3,474.50-4,245.65 kcal/kg. The densities range 0.45-0.78 g/cm3. The ash contents range 1.06-5.00 by wt.%. The shatter indexes range 0.71-0.93. The ignition times range 5.6-9.8 min. The combustion times range 30-96 min. The combustion rates range 1.38-1.74 g/min. The RDF with 1.0:20.0 water to rubber ratio yields the best efficiency, with 7.68% moisture content and 5.00% ash content. This complies with the local product standard of RDF. It yields 4,226.59 kcal/kg. of heating value. The heavy metal contents from the ash of RDF are within the standard. From the cost and profit analysis, making RDF from cassava rhizome can yield 504.22 baht/rai profit, while selling the rhizome directly yields 199.32 baht/rai profit.
GRAPHICAL ABSTRACT
HIGHLIGHTS
- This research result provides new knowledge, which is the use of Latex Rubber as a binder in making RDF.
- This research result allows rubber farmers to earn more income from selling RDF from rubber tree branches.
References
A. Białowiec, M. Micuda, J.A. Koziel,Waste to Carbon: Densification of Torrefied Refuse-Derived Fuel, Energies.11(11) (2018) 3233. 10.3390/en11113233.
C. Nobre, C. Vilarinho, O. Alves, B. Mendes, M. Gonçalves, Upgrading of refuse-derived fuel through torrefaction and carbonization: Evaluation of RDF char fuel properties, Energy.181 (2019) 66-76.
M. Kara, Environmental and economic advantages associated with the use of RDF in cement kilns, Resources, Conservation and Recycling. 68 (2012) 21-28.
H. Rezaei, F. Yazdan Panah, C.J. Lim, S. Sokhansanj, Pelletization of refuse-derived fuel with varying compositions of plastic, paper, organic and wood, Sustainability. 12(11) (2020) 4645. 10.3390/su12114645
R. García, M. D. P. González-Vázquez, F. Rubiera, C. Pevida, M. V. Gil, Co- pelletization of pine sawdust and refused derived fuel (RDF) to high-quality waste-derived pellets, Journal of Cleaner Production. 328 (2021) 129635. 10.1016/j.jclepro.2021.129635
W. Supranee, T. Nuchlee, Study of Energy Fuel Briquettes production from Sawdust of Rubber Wood and Animal Dung, UTK RESEARCH JOURNAL. 9 (2018).
C. Kumpapai, N. Boonthanom, T. Rodjananon, J. Wongthanate, The Efficiency Comparison of Fuel Briquettes from Agricultural Wastes, The Journal of Industrial Technology. 16(3) (2020) 28-38.
I. Batool, S. Munir, A. Khalid, A. Tahir, Potential Effectiveness of Different RDF Binders from Agro Waste, Technical Journal of University of Engineering & Technology Taxila. 26(1) (2021).
K. Paopongpaiboon, K. Boonserm, V. Horsakulthai, Development of mechanical and physical properties of charcoal briquettes from rubber seeds mixed with coconut shells as alternative energy, Journal of Engineering and Innovation. 16(1) (2023) 158-167.
Y. Yang, R. K. Liew, A. M. Tamothran, S. Y. Foong, P. N.Y. Yek, P. W. Chia, T. V. Tran, W. Peng, S. S. Lam, Gasification of refuse-derived fuel from municipal solid waste for energy production: a review, Environmental chemistry letters.19 (2021) 2127-2140. 10.1007/s10311-020-01177-5
N. Tangmankongworakoon, The production of fuel briquettes from bio-agricultural wastes and household wastes, Journal of Science and Technology. 12 (2014) 66-77.
C. Kumpapai, N. Boonthanom, T. Rodjananon, J. Wongthanate, The Efficiency Comparison of Fuel Briquettes from Agricultural Wastes, The Journal of Industrial Technology. 16(3) (2020) 28-38.
ASTM Standard D5865 International. (2013). Standard Test Method for Moisture in the Analysis Sample of Coal and Coke. ASTM International.
ASTM Standard D3173 International. (2013). Standard Test Method for Moisture in the Analysis Sample of Coal and Coke. ASTM International.
A. Awgichew, R. Nuguse, Development of Animal Feed Pellet Making Machine,Development. 7(1) (2024) 135-145.
N. Srisaeng, N. Tippayawong, K. Y. Tippayawong, Energetic and economic feasibility of RDF to energy plant for a local Thai municipality, Energy Procedia. 110 (2017) 115- 120.
Aliyu, M., et al. Production of composite briquettes (orange peels and corn cobs) and determination of its fuel properties. 2020. CIGR.
ASTM Standard D3174 International. (2013). Standard Test Method for Moisture in the Analysis Sample of Coal and Coke. ASTM International.
N. Tanpaiboonkul, T. Budnumpetch, Molding and Binding Method on Properties of Fuel from Water Hyacinth, Veridian E-Journal, Science and Technology Silpakorn University. 3(6) (2016) 86-100.
V. Thathong, N. Tantamsapya, C.Yossapol, C. H. Liao, W. Wirojanagud, S. Padungthon, Role of Colocasia esculenta L. schott in arsenic removal by a pilot-scale constructed wetland filled with laterite soil, Heliyon. 5(2) (2019). 10.1016/j.heliyon.2019.e01233
W. Punin, Development of Briquette Fuel from Co-Production of Corn Cob Charcoal and Low-Grade Coal Lignite Rejects, Burapha Science Journal. 23(1) (2018) 146-163.
S. Kittikorn Sasujit, S. Warapong, W. Nattapong, D. Natthawud, Study of Process Densification of Corn Cob and Corn Husk Briquettes by Cold Extrusion Technique Using Starch with Lime Mixed as Binder, Thaksin. J..8 (1) (2015) 5-14.
T. Gebreegziabher, A.O. Oyedun, H.T. Luk, T.Y.G. Lam, Y. Zhang, C.W. Hui, Design and optimization of biomass power plant, Chemical Engineering Research and Design. 92(8) (2014) 1412-1427.
S. M. Shafie, T. M. I. Mahlia, H. H. Masjuki, A. Ahmad-Yazid, A review on electricity generation based on biomass residue in Malaysia, Renewable and Sustainable Energy Reviews. 16(8) (2012) 5879-5889.
L. Thep-On, S. Chowdhury, K. A. Taechato, A. Kumar, I. Chanakaewsomboon, Optimization of biomass fuel composition for rubber glove manufacturing in Thailand, Sustainability. 14(19) (2022) 12493.
V. Van Giau, T.T. Kien, T. Van Thanh, T.T Hieu, N.T.P. Thao, L.T. Son, T.L. Luu, H. Schnitzer, L.T. Hai, The role of specific energy consumption in a heat recovery system for cassava starch production using an integrated agro-industrial system, Energy, Sustainability and Society. 14(1) (2024) 43.
N. Mohan, A.K. Kanaujia, Biomass energy for economic and environmental sustainability in India, Sugar Tech. 21(2) (2019) 197-201.
Thai Industrial Standards Institute (TISI), M.o.I., SOLID BIOFUELS - BIOMASS PELLET 2019.
A. Ussawarujikulchai, C. Semsayun, N. Prapakdee, N. Pieamsuwansiri, N. Chuchat, Utilization of durian and mangosteen peels as briquette fuel, 49 th Kasetsart University Annual Conference, Bangkok (Thailand). 1-4 Febuary 2011.
L. Nyathi, G. Charis, M. Chigondo, M. Maposa, D. Nyadenga, K. Nyenyayi, Fabrication of sawdust briquettes using local banana pulp as a binder, Detritus. 19 (2022) 84-93. 10.31025/2611-4135/2022.15193
R. N. P. Kiattisak, S. Tussanee, M. Chaiyoot, R. Polphat, Prototype System for Production of Refuse Derived Fuel (RDF-5) from Municipal Solid Waste Using Natural Rubber as Binder, ASEAN Journal of Scientific and Technological Reports. 26(3) (2023) 63-71. 10.55164/ajstr.v26i3.249665
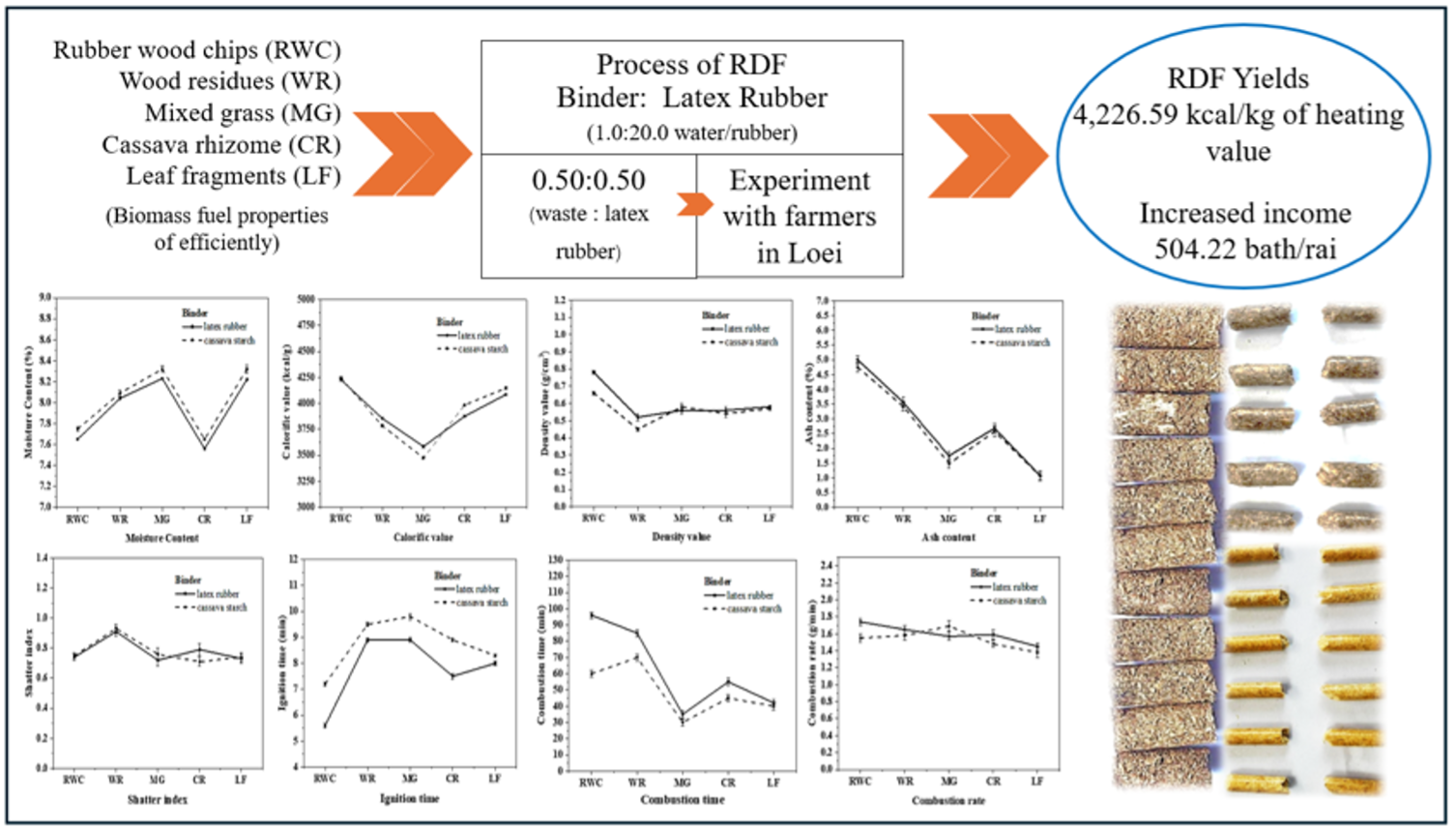
Downloads
Published
How to Cite
Issue
Section
Categories
License
Copyright (c) 2024 Creative Science

This work is licensed under a Creative Commons Attribution-NonCommercial-NoDerivatives 4.0 International License.