Investigation of transfer correction for in-service inspection of coated steel welds using ultrasonic method
Abstract
Welding is commonly used for fabricating tanks or piping systems, and the weld joints are inspected immediately without painting. After all welds have passed the acceptance criteria, the welds are painted to prevent corrosion. Oil and gas pipelines, fuel tanks and associated steel structures are prone to stress and corrosion during operation. Additionally, unforeseen events such as accidents, earthquakes, or plate movements may result in damage, leading to leaks and cracks that can have significant environmental implications. Annual or periodic inspections are essential, as they require the removal of paint for evaluation because sound waves are attenuated by the paint layer. However, paint stripping is a costly and time-consuming process. This study aims to investigate the appropriate transfer correction for compensating the ultrasonic energy attenuation caused by coating thickness at different frequencies and probe angles for in-service inspection of coated steel weld joints using the ultrasonic method. Carbon steel A36 was used as the calibration specimen according to ASME 2021 criteria. Alkyd resin enamel paint was sprayed onto the specimens to simulate coating layers ranging from 0-900 microns in thickness. Weld joints were also used to simulate a lack of fusion discontinuity, with a design coating thickness of 0-400 microns. This study utilized frequencies of 2.25, 5 and 10 MHz, and the chosen angles included the normal angle (0 degrees) and angles of 45, 60 and 70 degrees. Increasing coating layer thickness resulted in greater energy attenuation and reflected energy when the coating layer was more than half of the sound wavelength. Attenuation was not observed in the normal probe at 2.25 MHz. However, at frequencies of 5 and 10 MHz, attenuation was observed starting from the designed coating thickness of 500 and 100 microns, respectively. Attenuation was present at all frequencies and angles for angle probes, increasing with angle and frequency. Equations and transfer corrections were provided to compensate for energy attenuation due to coating layers, thereby improving the accuracy of signal testing for weld joints in industrial applications. It may be possible to develop more reliable testing methods to ensure the safety and integrity of fuel transportation systems without the need for costly and time-consuming paint removal.
References
Library of congress. (n.d.). Modes of Transportation. Oil and Gas Industry: A Research Guide. Retrieved September 10, 2022, from https://guides.loc.gov/oil-and-gas-industry/midstream/modes
Mohitpour, M. (2008). Energy supply and pipeline transportation: challenges and opportunities: an overview of energy supply security and pipeline transportation. New York, USA: ASME Press.
MAN energy solutions. (2021). Hydrocarbons. Germany. Retrieved September 10, 2022, from https://www.man-es.com/discover/decarbonization-glossary---man-energy-solutions/hydrocarbons
Kultida, B. (2019). The overview of carbon credit market in Thailand, Sau journal of science & technology, 5, 1-9. Retrieved September 13, 2022, https://ph01.tci-thaijo.org/index.php/saujournalst/ article/view/184556
TGO. (n.d.). Monitoring and reporting guideline for Thailand voluntary emission trading scheme (Thailand v-ets): Refinery and petrochemical industry sector v.0.2. Thailand. Retrieved September 13, 2022, from http://carbonmarket.tgo.or.th/admin/uploadfiles/ebook/content/ a539e6a236/index.html
PPT Public Company. (2015). Natural gas pipeline installation. Thailand.
PPT Public Company. (2014). Natural gas everyday. Thailand. Retrieved September 10, 2022, from https://www.pttplc.com/th/Media/Publications/Knowledge/Naturalgasknowledge.aspx
TOA-Chugoku paint. (n.d.). Epoxy Tank Coating. Retrieved May 24, 2022, from https://www.toa-chugoku.com
Mahesh, L. K. S. (2009). Ultrasonic Non Destructive Testing. Retrieved July 15, 2022, from https://www.researchgate.net/publication/262809705
American welding society. (2020). Structural welding code - steel (24th ed). USA: American Welding Society.
API. (2004). Recommended practice for ultrasonic and magnetic examination of offshore structural fabrication and guidelines for qualification of technicians. Washington, D.C., USA: American Petroleum Institute.
Predoi, M.V. & Petre, C.C. (2015). Thin Wall Pipe Ultrasonic Inspection Through Paint Coating, International Congress on Ultrasonics, 2015, Physics Procedia, 70(2015), 287-291.
Crowley, B.M. (2018). Ultrasonic Attenuation of Bridge Steels and Narrow-gap Improved Electroslag Welds, Master of Science in Civil Engineering Thesis. Indiana, USA: Purdue University.
Ono, K. (2020). A Comprehensive Report on Ultrasonic Attenuation of Engineering Materials, Including Metals, Ceramics, Polymers, Fiber-Reinforced Composites, Wood, and Rocks, Applied Sciences, 10, 7, pp. 2230.
Sankara, P. (2014). Corrosion Control in the Oil and Gas Industry. London, UK: Gulf Professional Publishing.
ASME boiler and pressure vessel committees (2021). Boiler and pressure vessel code section V-nondestructive examination. New York, USA: American Society of Mechanical Engineers.
Berke, M. (2000). Nondestructive Material Testing with Ultrasonics - Introduction to the Basic Principles, e-Journal of Nondestructive Testing (eJNDT), 5(9). Retrieved July 23, 2022, from https://www.ndt.net/?id=540
Olympus IMS (n.d.). Ultrasonic Flaw Detection Tutorial. Retrieved July 23, 2022, from https://www.olympus-ims.com/en/ndt-tutorials/flaw-detection/common-test-practices/
Center of nondestructive evaluation (n.d.). Waves. Retrieved August 28, 2022, from https://www.nde-ed.org/Physics/Waves/WaveInterference.xhtml
ASM International Handbook Committee. (1989). ASM Handbook Volume 17: Nondestructive Evaluation and Quality Control. Ohio, USA: ASM International.
Peter, J. Sh. (2001). Nondestructive Evaluation: Theory, Techniques, and Applications. New York, USA: Marcel Dekker, Inc.
Cheeke, J. D. N. (2002). Fundamentals and Applications of Ultrasonic waves. Florida, USA: CRC Press LLC.
Steven, L. G. (2020). Understanding Acoustics: An Experimentalist’s View of Sound and Vibration (2nd ed), ASA Press.
Ed, G., Robert, G., & Rick, M. (2016). Low velocity elastomer polymer wedges applied to TOFD, e-Journal of Nondestructive Testing (eJNDT), 21(5), 1-8. Retrieved October 5, 2022, from http://www.ndt.net/?id=19090
Robinson, E. A., & Sven, T. (2008). Digital imaging and deconvolution: the ABCs of seismic exploration and processing, Tulsa, Oklahoma, USA: Society of Exploration Geophysicists.
Boumerzoug, Z., Derfouf, C., & Baudin, T. (2010). Effect of welding on microstructure and mechanical properties of an industrial low carbon steel. Engineering, 2, 502-506. Retrieved September 15, 2022, from https://www.scirp.org/html/2246.html
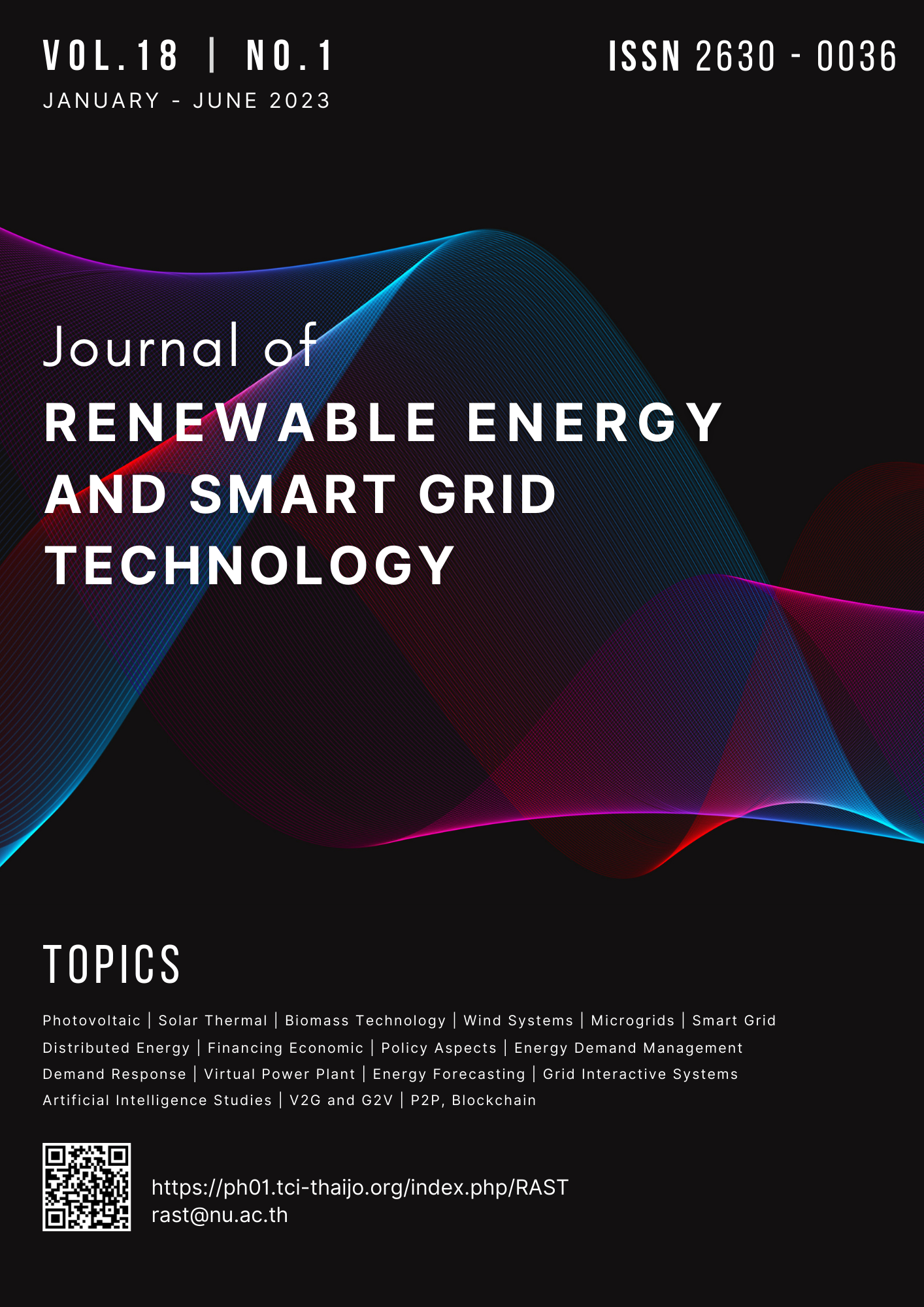
Downloads
Published
How to Cite
Issue
Section
License
Copyright (c) 2023 School of Renewable Energy and Smart Grid Technology (SGtech)

This work is licensed under a Creative Commons Attribution-NonCommercial-NoDerivatives 4.0 International License.
All copyrights of the above manuscript, including rights to publish in any media, are transferred to the SGtech.
The authors retain the following rights;
1. All proprietary rights other than copyright.
2. Re-use of all or part of the above manuscript in their work.
3. Reproduction of the above manuscript for author’s personal use or for company/institution use provided that
(a) prior permission of SGtech is obtained,
(b) the source and SGtech copyright notice are indicated, and
(c) the copies are not offered for sale.