Machinability of tool steels machined by electric-discharge machining
DOI:
https://doi.org/10.55674/snrujst.v14i1.244172Keywords:
Electric-discharge machining (EDM), Machinability, Tool steel, SKD11, DC53Abstract
SKD11 has been a widely used tool steel for cold works for many years while DC53 tool steel is intently developed to replace SKD11. In this paper, the machinability of these two tool steels was compared in terms of material removal rate (MRR), electrode wear ratio (EWR), and arithmetic mean of value of roughness (Ra) of the specimen machined by electric-discharge machining. The machining variables involved were electric-discharge time and electric-discharge peak current. The machining electrode was made from a copper alloy. Results show that both electric-discharge time and electric-discharge peak current had an influential effect on MRR, EWR, and Ra of both tool steels. MRR of SKD11 was significantly higher than that of DC53 while DC53 caused higher EWR than SKD11. It was found that SKD11 provided a better surface finish than DC53. Empirical models for MRR, EWR, and Ra were also presented in this paper.
References
Coldwork_properties, https://www.daido.co.jp/en/pr oducts/tool/cold/index.html, 15 March 2021.
S. Chuvaree, K. Kanlayasiri, An investigation on dimensional accuracy of EDM deep hole using multi-hole interior flushing electrode, MATEC Web Conf.
(2018) 1 – 4.
S.K. Ramuvel, S. Paramasivam, Study on tool steel
machining with ZNC EDM by RSM, GREY and
NSGA, J. Mater. Res. Technol. 9 (2020) 3885 – 3896.
H. El-Hofy, Advanced Machining Processes: Nontraditional and hybrid machining processes, First
edition, McGraw-Hill, New York, 2005.
R. Snoyes, F. Van Dijck, Plasma channel diameter
growth affects stock removal, CIRP Annals. 21 (1972)
– 40.
S.M. Pandit, K.P. Rajurkar, A stochastic approach to
thermal modeling applied to electro-discharge
machining, J. Heat Transfer. 105 (1983) 555 – 562.
P.C. Pandey, S.T. Jilani, Plasma channel growth and the resolidified layer in EDM, Precis. Eng. 8 (1986)
– 110.
P. Shankar, V.K. Jain, T. Sundarajan, Analysis of
spark profile during EDM process, Mach. Sci.
Technol. 1 (1997) 195 – 217.
Y.H. Guu, H. Hocheng, Improvement of fatigue life
of electrical discharge machined AISI D2 tool steel by TiN coating, Mater. Sci. Eng. A. 318 (2001) 155 – 162.
S. Jeelani, M.R. Collins, Effect of electric discharge machining on the fatigue life of Inconel 718, Int. J. Fatigue. 10 (1988) 121 – 125.
O.A.A. Zeid, On the effect of electrodischarge machining parameters on the fatigue life of AISI D6 tool steel, J.Mater. Process. Technol. 68 (1997) 27 – 32.
A. Ramulu, G. Paul, J. Patel, EDM surface effects on the fatigue strength of a 15 vol% SiCp/Al metal matrix composite material, Compos. Struct. 54 (2001) 79 – 86.
I. Puertas, C.J. Luis, L. Alvarez, Analysis of the influence of EDM parameters on surface quality, MRR and EW of WC–Co, J. Mater. Process. Technol. 153–154 (2004) 1026 – 1032.
Y.H. Guu, H. Hocheng, C.Y. Chou, C.S. Deng, Effect of electrical discharge machining on surface characteristics and machining damage of AISI D2 tool steel, Mater. Sci. Eng. A. 358 (2003) 37 – 43.
H. Ramaswamy, L. Blunt, Effect of EDM process parameters on 3D surface topography, J. Mater. Process. Technol. 148 (2004)155 – 164.
S.L. Chen, S.F. Hsieh, H.C. Lin, M.H. Lin, J.S. Huang, Electrical discharge machining of TiNiCr and TiNiZr ternary shape memory alloys, Mater. Sci. Eng. A. 445 – 446 (2007) 486 – 492.
Physical properties of tool steel, https://www.steelgr.com/Steel-Grades/Mould-Steel, 27 February 2021.
J.C. Rebelo, A.M. Dias, D. Kremer, J.L. Lebrun, Influence of EDM pulse energy on the surface
integrity of martensitic steels, J. Mater. Process.
Technol. 84 (1998) 90 – 96.
J.C. Rebelo, A.M. Dias, R. Mesquita, P. Vassalo,
M. Santos, An experimental study on electro- discharge machining and polishing of high strength copper-beryllium alloys, J. Mater. Process. Technol. 103 (2000) 389 – 397.
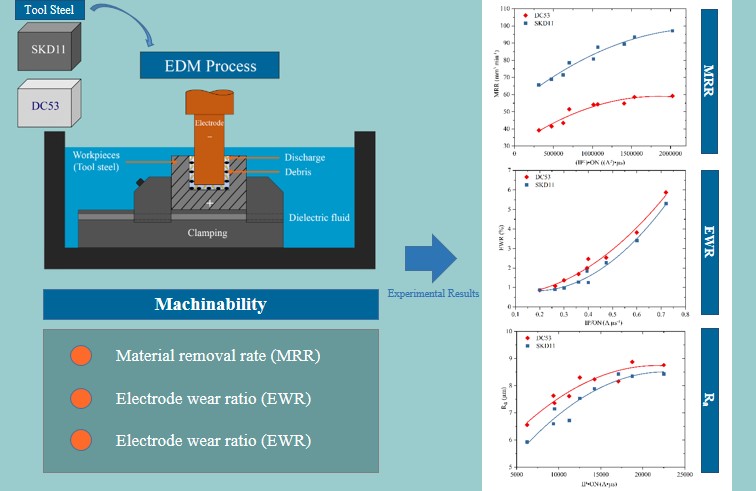
Downloads
Published
How to Cite
Issue
Section
License
Copyright (c) 2022 SNRU Journal of Science and Technology

This work is licensed under a Creative Commons Attribution-NonCommercial-NoDerivatives 4.0 International License.