Study of the temperature to render fat down affecting the biodiesel yield from cow fat by the transesterification reaction method
DOI:
https://doi.org/10.55674/jmsae.v12i2.249955Keywords:
Biodiesel, Transesterification, Cow fat, Render fat downAbstract
Animal fats are high in saturated fatty acids, so they are useful in the part of soap making, including biodiesel oils. Its advantage is high heating and low cost. The aim of this research was to study the temperatures to render fat down from cow fat at 150 °C, 200 °C, 250 °C, 300 °C, and 350 °C, ±2 °C affecting the biodiesel oil yield. The transesterification reaction biodiesel production by using the base catalyst including Methanol (CH3OH) and Sodium hydroxide (NaOH). The reaction temperature was controlled at 50 °C. The experiment is carried out with a biodiesel reactor consisting of the rendered set, catalyst mixing tank, and heating set to get rid of water from biodiesel. The trend toward the increased temperature to render fat down also affected the higher FFA and a temperature of 350 °C, this resulted in a higher range of 2.53% of the FFA. The result was found that the optimum temperature for rendering fat down was 250 °C and the biodiesel oil yield was 75.50% by volume, the HHV had a maximum of 41.17 MJ kg–1, and viscosity of 4.60 cSt. Furthermore, it illustrated that the temperature to render fat down that is too high will affect to decrease the biodiesel yield but increase glycerin content.
References
J.V. Gerpen, B. Shanks, R. Pruszko, Biodiesel Production Technology, NREL. (2004) 510 – 36244.
S.N. Gebremariam, J.M. Marchetti, Economics of biodiesel production – a Review, Energ Convers Manag. 168 (2018) 74 – 84.
J.M. Marchetti, V.U. Miguel, A.F. Errazu, Possible methods for biodiesel production, Renewable Sustainable Energy Rev. 11 (2007) 1300 – 1311.
O. Sangnate, P. Reubroycharoen, Maximum blended ration of pyrolysis oil for thai commercial diesel standard, J-REC. 3 (2020) 39 – 45.
A. Demirbas, Importance of biodiesel as transportation fuel, Energy Policy. 35 (2007) 4661 – 4670.
D. Singh, D. Sharma, S.L. Soni, S. Sharma, P. Kumar Sharma, A. Jhalani, A review on feedstocks production processes and yield for different generations of biodiesel, Fuel. 262 (2020).
G. Knothe, Analyzing Biodiesel: Standards and other methods, JAOCS. 83 (2006) 823 – 833.
M. Balat, H. Balat, Progress in biodiesel processing, Appl Energ. 87 (2010) 1815-1835.
F. Ma, M. A. Hannab, Biodiesel production a review, Bioresour Technol. 70 (1999) 1 – 15.
R.G. Nelson, M.D. Schrock, Energetic and economic feasibility associated with the production, processing, and conversion of beef tallow to a substitute diesel fuel, Biomass Bioenergy. 30 (2006) 584 – 591.
J.V. Gerpen, Biodiesel processing and production, Fuel Process. Technol. 86 (2005) 1097 – 1107.
Y.C. Sharma, B. Singh, S.N. Upadhyay, Advancements in development and characterization of biodiesel: A review, Fuel. 87 (2008) 2355 – 2373.
Y.C. Sharma, B. Singh, Development of biodiesel: Current scenario, Renewable Sustainable Energy Rev. 13 (2009) 1646 – 1651.
H. Bhatti, M. Hanif, M. Qasim, Ataurrehman, Biodiesel production from waste tallow, Fuel. 87 (2008) 2961 – 2966.
C. Oner, S. Altun, Biodiesel production from inedible animal tallow and an experimental investigation of its use as alternative fuel in a direct injection diesel engine, Appl Energ. 86 (2009) 2114 – 2120.
P. Kosiyanant, W. Tangcharoenchai, Characteristics of tallow fractionates from two different breeds, KMUTNB. 20 (2010) 125 – 131.
U. Thawornchaisit, C. Chanyod, P. Intaprom, W. Euengmongkhonchai, Biodiesel production from beef fats by based-catalyzed transesterification reaction, Science KMITL. 25 (2016) 88 –98.
I.M. Atadashi, M.K. Aroua, A.R. Abdul Aziz, N.M.N. Sulaiman, Production of biodiesel using high free fatty acid feedstocks, Renewable Sustainable Energy Rev.16 (2012) 3275 –3285.
A.Kongsen,R.Pairintra,K.Sudaprasert,W.Limmun,Free fatty acid in Vegetable oil and animal fat during storage, Agricultural Sci. J. 45(2) (2014) 261-264.
S. Panpraneecharoen, S. Chumanee, W. Pongpian, R. Khoomsab, Study the optimal conditions for biodiesel production, JSTPCRU. 3 (2018) 1-12.
R.K. Saluja, V. Kumar, R. Sham, Stability of biodiesel –A review, Renew Sustain Energy Rev. 62 (2016) 866–881.
A.P. Soares Dias, M. Ramos, M. Catarino, J. Puna, J. Gomes, Solvent assisted biodiesel production by co-processing beef tallow and soybean oil over calcium catalysts, Waste Biomass Valorization. 11 (2019)6249–6259.
U. Sai Akhil, A. Alagumalai, A short review on valorization of slaughterhouse wastes for biodiesel production, ChemistrySelect. 4 (2019) 13356–13362.
B. Esther Olubunmi, A. Fatai Alade, S. Ogbeide Ebhodaghe, O. Tokunbo Oladapo, Optimization and kinetic study of biodiesel production from beef tallow using calcium oxide as a heterogeneous and recyclable catalyst, Energy Convers Manag. 14 (2022) 100221.
A.P. Soares Dias, M. Ramos, B. Rijo, Rendering of Beef Tallow for Biodiesel Production: Microwave versus boiling water and acetone fat extraction, Processes. 10 (2022) 666.
H. Prima Astuti, A. Izkinal, R. Dwi, Optimization of biodiesel production from beef tallow using microwave assisted, Journalof Advanced Research in Fluid Mechanics and Thermal Sciences. 97 (2022) 57–65.
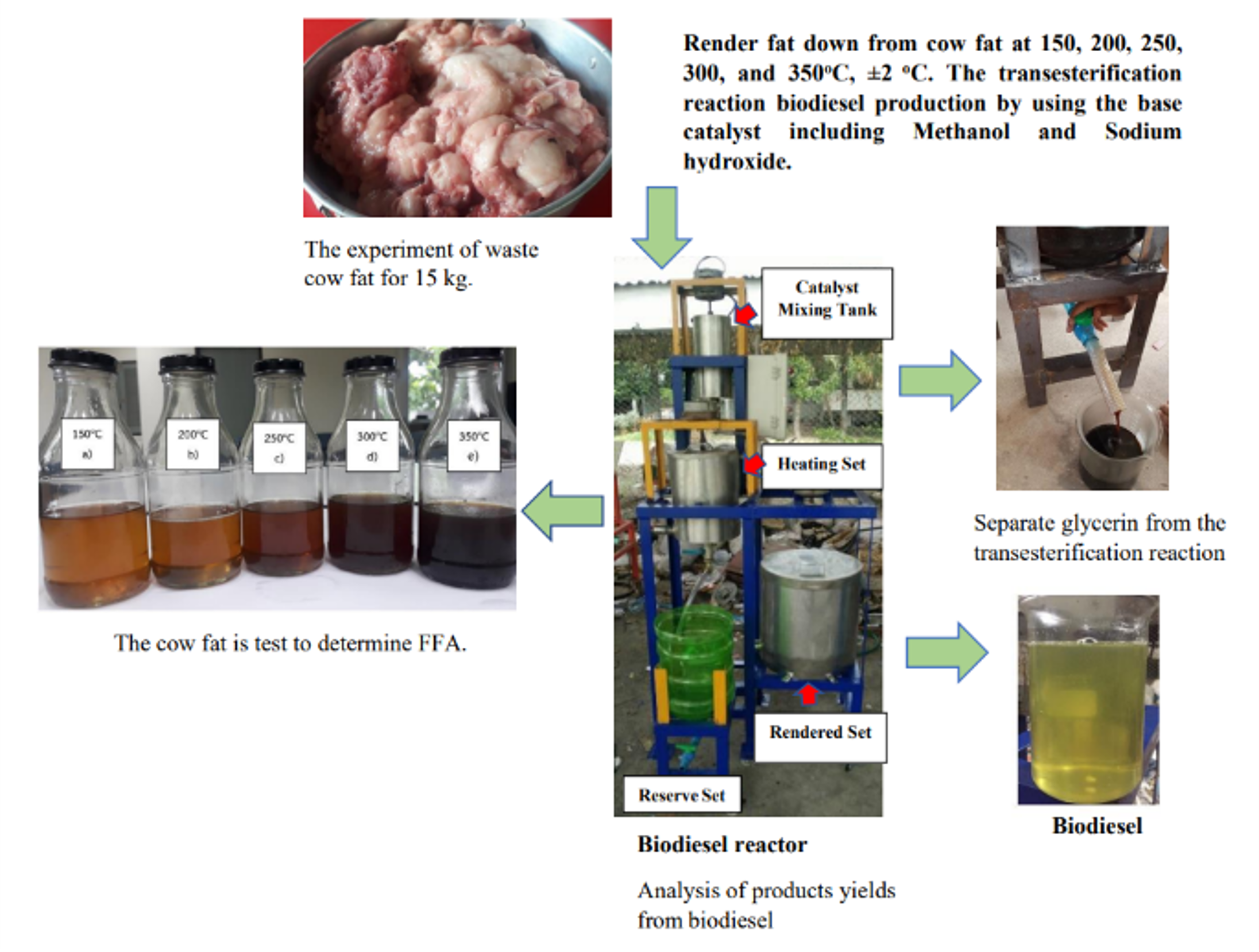
Downloads
Published
How to Cite
Issue
Section
License
Copyright (c) 2023 Journal of Materials Science and Applied Energy

This work is licensed under a Creative Commons Attribution-NonCommercial-NoDerivatives 4.0 International License.