Techno-Economic Assessment between Traditional and Fused Deposition Modeling- based Additive Manufacturing Technology
DOI: 10.14416/j.ind.tech.2024.12.007
Keywords:
Cost Analysis, Traditional Manufacturing Technology, Additive Manufacturing Technology, Fused Deposition Modeling, Healthcare ComponentAbstract
Additive manufacturing (AM) or 3D printing (3DP) is widely used in production processes and product design nowadays as 3DP can not only reduce waste generated by traditional manufacturing methods but also allow for more efficient use of materials. Accordingly, analyzing the cost-effectiveness and techno-economic assessment of 3DP in various contexts is crucial for enhancing competitiveness. In this research, we aim to study and compare the technology and production costs of medical products, specifically finger splints, produced by traditional methods and 3DP technology by assessing the machine cost, material cost, and labor cost, respectively. The traditional manufacturing based on the injection method is found to have high manufacturing costs due mainly to the mold design and fabrication, in which economies of scale are needed with the increase in manufacturing quantity. In addition, production using AM technology is analyzed following the designed experiment and the aid of the Cura platform to assess the technical and manufacturing cost for the FDM method with one and five healthcare workpieces each time. Finally, the cost analysis and breakeven point are investigated, where manufacturing one and five workpieces using FDM-based AM technology is found to be comparable to producing 2,264 and 17,123 pieces using traditional, injection manufacturing, respectively. The results from the analysis in this study are expected to be practically used as a guideline for selecting diverse production technologies and production scheduling involving traditional and AM technologies.
References
A. Khaira, From 3D to 4D: The evolution of additive manufacturing and Its Implications for Industry 5.0, Emerging Technologies in Digital Manufacturing and Smart Factories, IGI Global, PA, USA, 2024, 39-53.
https://www.precedenceresearch.com/3d-printing-in-healthcare-market. (Accessed on 5 January 2024)
K. Ransikarbum, R. Pitakaso, N. Kim and J. Ma, Multicriteria decision analysis framework for part orientation analysis in additive manufacturing, Journal of Computational Design and Engineering, 2021, 8(4),1141-1157.
K. Ransikarbum and R Leksomboon, Analytic hierarchy process approach for healthcare educational media selection: Additive manufacturing inspired study, 8th IEEE International Conference on Industrial Engineering and Applications (ICIEA), Proceeding, 2021, 154-158.
K. Ransikarbum, R. Pitakaso and N. Kim, A decision-support model for additive manufacturing scheduling using an integrative analytic hierarchy process and multi-objective optimization, Applied Sciences, 2020, 10(15), 5159.
K. Ransikarbum, S. Ha, J. Ma and N. Kim, Multi-objective optimization analysis for part-to-Printer assignment in a network of 3D fused deposition modeling, Journal of Manufacturing Systems, 2017, 43, 35-46.
M. D. Monzon, Z. Ortega, A. Martínez and F. Ortega, Standardization in additive manufacturing: activities carried out by international organizations and projects, The International Journal of Advanced Manufacturing Technology, 2014, 76(5-8), 1111-1121.
O. Abdulhameed, A. Al-Ahmari, W. Ameen, and S. H. Mian, Additive manufacturing: Challenges, trends, and applications, Advances in Mechanical Engineering, 2019, 11(2), 1-27.
B. Westerweel, R.J.I. Basten and G.-J. van Houtum, Traditional or additive manufacturing? Assessing component design options through lifecycle cost analysis, European Journal of Operational Research, 2018, 270(2), 570-585.
T. Pereira, J. V. Kennedy and J. Potgieter, A comparison of traditional manufacturing vs additive manufacturing, the best method for the job, Procedia Manufacturing, 2019, 30, 11-18.
R.S. Arulmozhi, M. Vaidya, M.G. Poojalakshmi, D.A. Kumar, and K. Anuraag, 3D Design and printing of custom-fit finger splint, Biomedical Engineering: Applications, Basis and Communications, 2018, 30(05). 1850032.
S.L. Teng, Y.R. Wong, P.P.H. Lim, and D.A. McGrouther, An adjustable and customised finger splint to improve mallet finger treatment compliance and outcomes, Annals of 3D Printed Medicine, 2024, 13, 100142.
https://www.crealitycloud.com/model detail/6528f436657358aaf3f3dc7e source=20&isFree=false&objId=111 (Accessed on 15 March 2024)
https://adecco.co.th/salary-guide (Accessed on 15 March 2024)
H.S. Nam, C.H. Seo, S.Y. Joo, D.H. Kim, and D.S. Park, The Application of three-dimensional printed finger splints for post hand burn patients: A Case Series Investigation, Annals of Rehabilitation Medicine, 42(4), 2018, 634-638.
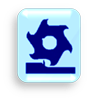
Downloads
Published
Issue
Section
License
Copyright (c) 2024 https://ojs.kmutnb.ac.th/index.php/joindtech/article/view/7449

This work is licensed under a Creative Commons Attribution-NonCommercial-NoDerivatives 4.0 International License.
ผลงานวิจัยและบทความวิชาการที่ปรากฏในวารสารนี้ เป็นความคิดเห็นอิสระของผู้เขียน ผู้เขียนจะต้องเป็นผู้รับผิดชอบต่อผลทางกฎหมายใด ๆ ที่อาจจะเกิดขึ้นจากบทความนั้น กองบรรณาธิการและคณะจัดทำวารสารฯไม่จำเป็นต้องเห็นด้วยเสมอไป