An Optimization Process of Automatic Finishing Surface Treatment Al 7075 by a Single Roller Burnishing Tool
DOI: 10.14416/j.ind.tech.2024.08.009
Keywords:
Roller burnishing, surface hardness, surface roughness, Finishing process of Al 7075Abstract
This research designed and developed a single-roller burnishing tool for the automatic finishing surface of 7075 aluminum alloy (Al 7075). The conventional finishing process for such materials requires complex processes such as turning, grinding, and polishing. In addition, the turning process cannot achieve a surface finish with a low roughness. Therefore, the purpose of this research aims to design and fabricate a single-roller burnishing tool that can be installed on a CNC lathe. In addition, the research will study the fundamental mechanisms of surface finishing improvement using a single-roller burnishing tool on Al 7075 and study the parameters that affect the surface quality of Al7075 by combining two automatic processes. This process includes turning and roller Burnishing, which will reduce the complex steps in surface finishing. In the experiment, the following parameters were used in the roller burnishing process: three levels of constant spring force 150, 300, and 450 Newtons, feed rate 0.05, 0.1, and 0.15 mm/rev, and rotational speed 600 and 1,200 rpm. The results of the experiment showed that the feed rate was the main factor that affected the surface roughness of the workpiece with a statistical significance of 95%. The best feed rate was 0.05 mm/rev, which resulted in a surface roughness of 0.078 µmRa. The surface roughness after the turning process was 0.371 µmRa, which means that the surface roughness was reduced about 4-5 times. In addition, the hardness of Al 7075 after roller burnishing increased by 34%. This shows that the process not only improves the surface roughness quality but also increases the residual stress on the surface of the workpiece.
References
A survey of the status of the non-ferrous metals industry, aluminum, by the Center for Steel and Metals Industry Insight Analysisม Iron and Steel Institute of Thailand, 2014. (in Thai)
S. Ramesh, L. Karunamoorthy and K. Palanikumar, Measurement and analysis of surface roughness in turning of aerospace titanium alloy (gr5). Measurement, 2012, 45(5), 1266-1276.
M.V. Ramana and Y.S. Aditya, Optimization and influence of process parameters on surface roughness in turning of titanium alloy, Materials Today: Proceedings, 2017, 4(2), 1843-1851.
A. Yang, Y. Han, Y. Pan, H. Xing, and J. Li, Optimum surface roughness prediction for titanium alloy by adopting response surface methodology, Results in Physics, 2017, 7, 1046-1050.
J. P. Ajithkumar, and M.A. Xavior, Cutting force and surface roughness analysis during turning of Al 7075 based hybrid Composites, Procedia Manufacturing, 2019, 30, 180-187.
H. Basak and H.H. Goktas, Burnishing process on al-alloy and optimization of surface roughness and surface hardness by fuzzy logic, Materials and Design, 2009, 30(4), 1275-1281.
M. Okada, S. Suenobu, K. Watanabe, Y. Yamashita and N. Asakawa, Development and burnishing characteristics of roller burnishing method with rolling and sliding effects, Mechatronics, 2015, 29, 110-118.
V. Chomienne, F. Valiorgue, J. Rech, and C. Verdu, Influence of ball burnishing on residual stress profile of a 15-5PH stainless steel, CIRP Journal of Manufacturing Science and Technology, 2016, 13, 90-96.
A.S. Maheshwari and R.R. Gawande, Influence of stiff ball burnishing process parameters on surface roughness of AA 6063, International Journal of Applied Engineering Research, 2018, 13(8),30-35.
G.V. Duncheva, J.T. Maximov, V.P. Dunchev, A.P. Anchev, T.P. Atanasov, and J. Capek, Single toroidal roller burnishing of 2024-T3 Al alloy implemented as mixed burnishing process, The International Journal of Advanced Manufacturing Technology, 2020, 111, 3559-3570.
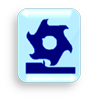
Downloads
Published
Issue
Section
License

This work is licensed under a Creative Commons Attribution-NonCommercial-NoDerivatives 4.0 International License.
ผลงานวิจัยและบทความวิชาการที่ปรากฏในวารสารนี้ เป็นความคิดเห็นอิสระของผู้เขียน ผู้เขียนจะต้องเป็นผู้รับผิดชอบต่อผลทางกฎหมายใด ๆ ที่อาจจะเกิดขึ้นจากบทความนั้น กองบรรณาธิการและคณะจัดทำวารสารฯไม่จำเป็นต้องเห็นด้วยเสมอไป