Hardness Improvement on Graphite by Silicon Nitride (Si3N4) Reinforcement using Slurry Infiltration
DOI: 10.14416/j.ind.tech.2024.08.003
Keywords:
Graphite, Si3N4 reinforcement, Infiltration, Hardness, Composite materialAbstract
Graphite was an attractive material for high-temperature applications, however, there was limited in its relatively low hardness. In this study, a reinforced graphite composite with Si3N4 was developed through infiltrating a silicon slurry onto the graphite surface. The slurry infiltration process was carried out for different durations: 5, 10, and 15 minutes, then sintered at a high temperature of 1,450 °C in a nitrogen atmosphere. The research revealed the presence of α-Si3N4 and β-Si3N4 particles in the microstructure of the graphite composite, with higher quantities observed after 15-minute infiltration. The Si3N4 reinforcement influenced the porosity of the graphite, resulting in a reduction in porosity and an increase in hardness by 53.98%, 140.18%, and 217.49% after infiltration durations of 5, 10, and 15 minutes, respectively. Notably, the maximum enhancement in hardness (217.49%) was achieved with Si3N4 reinforcement and a 15-minute infiltration, attributed to the effective dispersion of Si3N4 within the graphite porosity. This led to a remarkable increase in hardness, reaching a peak value of 15.07 GPa. The improvement in mechanical properties and the reinforcement with Si3N4 have significantly enhanced the hardness of the graphite composite, making it crucial for developing high-performance materials with abrasion resistance and increased mechanical strength.
References
T.D. Burchell and T.R. Pavlov, Graphite: Properties and characteristics, Comprehensive Nuclear Materials, 2020, 7, 355-381.
https://www.britannica.com/science/ graphite-carbon. (Accessed on 22 June 2023)
N.B. Dhokey and K.K. Rane, Wear behavior and its correlation with mechanical properties of TiB2 reinforced aluminium-based composites, Advances in Tribology, 2011, 2011, 837469.
M.A. Hernandez, K.D. Bakoglidis and P. Xiao, A new slurry infiltration method to enhance the wear resistance of bulk graphite with development of reinforced graphitic composites including SiC or Si3N4 hard particles, Journal of the European Ceramic Society, 2019, 39(6), 1984-1992.
H.S. Kim, On the rule of mixtures for the hardness of particle reinforced composites, Materials Science and Engineering, 2000, 289(1-2), 30-33.
J.Z. Jiang, F. Kragh, D.J. Frost, K. Ståhl and H. Lindelov, Hardness and thermal stability of cubic silicon nitride, Journal of Physics Condensed Matter, 2001, 13(22), 515-520.
P. Ge, Y. Cheng and K. Sun, Structure and performance of Si3N4/SiC/CNT composite fibres, Ceramics International, 2019, 45(10), 12677-12681.
A.K. Kothari, J. Kengqing, R. Janet and B.W. Sheldon, Comparison between carbon nanotube and carbon nanofiber reinforcements in amorphous silicon nitride coatings, Journal of the American Ceramic Society, 2008, 91(8), 2743–2746.
P. Sharma, S. Sharma and D. Khanduja, Production and some properties of Si3N4 reinforced aluminium alloy composites, Journal of Asian Ceramic Societies, 2015, 3(3), 352-359.
J.K. Kim, P.K. Rohatgi, J.O. Choi and C.O. Choi, Wear properties and effect of molds on microstructure of graphite reinforced copper alloy composites made by centrifugal casting, Metals and Materials International, 2005, 11(4), 333-340.
M. Chen, W. Zhou, J. Zhang and Q. Chen, Dielectric property and space charge behavior of polyimide/silicon nitride nanocomposite films, Polymers, 2020, 12(2), 322.
A. Khan, M. Puttegowda, P. Jagadeesh, H.M. Marwani, A.M. Asiri, A. Manikandan, A.A.P. Khan, G. Md Ashraf, S.M. Rangappa and S. Siengchin, Review on nitride compounds and its polymer composites: a multifunctional material, Materials Research and Technology, 2022, 18, 2175-2193.
I.E. Aparicio, D.T. Fishpool, V.R. Diaz, R.A. Dorey and J.A. Yeomans, Evaluation of polymer matrix composite manufacturing routes for production of an oxide/oxide ceramic matrix composite, Journal of the European Ceramic Society, 2022, 42(5), 2420-2428.
C. Wang, X. Wang, B. Wang, G. Xiao, R. Qiao, F. Zhang, Y. Bai, Y. Li, Y. Wu, Z. Wang and H. Wang, Enhancement of thermal shock resistance in B-Si3N4 coating with in situ synthesized β-Si3N4 nanowires/nanobelts on porous Si3N4 ceramics, Ceramics International, 2021, 47(18), 25449-25457.
Y. Tong, S. Bai, X. Liang, Q.H. Qin and J. Zhai, Reactive melt infiltration fabrication of C/C-SiC composite: Wetting and infiltration, Ceramics International, 2016, 42(15), 17174-17178.
X. Liu, D. Zhang, R. Ma, Y. Wang, X. Yang and Y. Liu, The two-tier tissue reinforcing and toughening mechanism caused by dual-granularity Si powders ingredient, and dielectric properties in reaction bonded and sintered reaction bonded Si3N4 porous ceramics, Ceramics International, 2022, 48(16), 22877-22884.
S. Li, H. Cui, Q. Ma, X. Liu, Y. Wang, L. Shang and Y. Zheng, The one-step pyrolysis process of rattan-based silicon carbide multiphase ceramics prepared by sol–gel method, Journal of Wood Science, 2021, 67(1), 58.
D. Kopeliovich, Advances in the manufacture of ceramic matrix composites using infiltration techniques, Advances in Ceramic Matrix Composites, 2014, 79-108.
M. Rosso, Ceramic and metal matrix composites: Routes and properties, Journal of Materials Processing Technology, 2006, 175(1-3), 364-375.
W. Guo, Y. Ye, S. Bai, L. Zhu and S. Li, Preparation and formation mechanism of C/C–SiC composites using polymer-Si slurry reactive melt infiltration, Ceramics International, 2020, 46(5), 5586-5593.
J. C. Margiotta, D. Zhang and D.C. Nagle, Microstructural evolution during silicon carbide (SiC) formation by liquid silicon infiltration using optical microscopy, Journal of Refractory Metals and Hard Materials, 2009, 28, 191-197.
J. Rakshit and P.K. Das, Optimization of time-temperature schedule for nitridation of silicon compact on the basis of silicon and nitrogen reaction kinetics, Bulletin of Materials Science, 2000, 23, 249–253.
H.M. Jennings and M.H. Richman, Structure, formation mechanisms and kinetics of reaction-bonded silicon nitride, Journal of Materials Science, 1976, 11, 2087–2098.
M. Long, Y. Li, H. Qin, W. Xue, J. Chen, J. Sun and R.V. Kumar, Formation mechanism of Si3N4 in reaction-bonded Si3N4-SiC composites, Ceramics International, 2016, 42(15), 16448-16452.
Y. Li, Q. Wang, H. Fan, S. Sang, Y. Li and L. Zhao, Synthesis of silicon carbide whiskers using reactive graphite as template, Ceramics International, 2014, 40(1), 1481-1488.
A. Saleem, Y. Zhang, H. Gong, M.K. Majeed, M.Z. Ashfaq, J. Jing, X. Lin and M. Sheng, Carbon nanostructure-reinforced SiCw/Si3N4 composite with enhanced thermal conductivity and mechanical properties, RSC Advances, 2020, 10(25), 15023–15029.
S. Larpkiattaworn, P. Ngernchuklin, W. Khongwong, N. Pankurddee and S. Wada, The influence of reaction parameters on the free Si and C contents in the synthesis of nano-sized SiC, Ceramics International, 2006, 32(8), 899-904.
M. Saito, S. Nagashima and A. Kato, Crystal growth of SiC whisker from the SiO(g)-CO system, Journal of Materials Science, 1992, 11, 373–376.
Y. H. Gao, Y. Bando, K. Kurashima and T. Sato, SiC nanorods prepared from SiO and activated carbon, Journal of Materials Science, 2002, 37(10), 2023–2029.
G. Ziegler, J. Heinrich and G. Wötting, Relationships between processing, microstructure and properties of dense and reaction-bonded silicon nitride, Journal of Materials Science, 1987, 22(9), 3041–3086.
H.M. Jennings, On reactions between silicon and nitrogen, Journal of Materials Science, 1983, 18(4), 951–967.
https://sm-nitk.vlabs.ac.in/exp/vickers-hardness-test/theory.html#:~:text=The%20corresponding%20units%20of%20HV,get%20the%20answer%20in%20GPa. (Accessed on 9 April 2024)
Q. Wu, Z. Huo, C. Chen, X. Li, Z. Wang, C. Wang, L. Zhang, Y. Gao, M. Xiong and K. Pan, Prediction of four Si3N4 compounds by first-principles calculations, AIP Advances, 2023, 13, 045310.
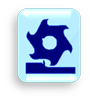
Downloads
Published
Issue
Section
License

This work is licensed under a Creative Commons Attribution-NonCommercial-NoDerivatives 4.0 International License.
ผลงานวิจัยและบทความวิชาการที่ปรากฏในวารสารนี้ เป็นความคิดเห็นอิสระของผู้เขียน ผู้เขียนจะต้องเป็นผู้รับผิดชอบต่อผลทางกฎหมายใด ๆ ที่อาจจะเกิดขึ้นจากบทความนั้น กองบรรณาธิการและคณะจัดทำวารสารฯไม่จำเป็นต้องเห็นด้วยเสมอไป