Study of Strength and Corrosion Behavior on Aluminum A1050 and Copper C1100 Joints by Mechanical Steel Bolt, Blind Steel Rivet, and Resistance Spot Weld
DOI: 10.14416/j.ind.tech.2024.08.001
Keywords:
Corrosion, Resistivity, Aluminum, Copper, Mechanical joining, Resistance spot weld, ANOVAAbstract
A1050 and C1100 are normally used as terminal tabs, they are connected either by mechanical joining, e.g. mechanical bolt, or rivet, or by welding, e.g. resistance spot welding. This study aimed to compare the mechanical bolt, blind rivet, and resistance spot welding methods by measuring important joining properties to support the process selection for joining terminal tabs in pouch cell batteries. T-peel-shaped were created and immersed in a 3.5 wt% NaCl electrolyte solution over different durations. Tensile tests were conducted to ascertain the maximum load-bearing capacity of the various joints. Furthermore, the electrical resistivities of the joints were measured using the 4-point probe technique. The corrosion rates of various joints were calculated from the corrosion current density (Icorr) measured from the Tafel polarization technique. ANOVA and Tukey’s test were used for analyst data comparison of the three joining techniques. Based on the mechanical properties, the mechanical joints by either steel bolt or steel rivet exhibited higher shear peeling strength than the resistance spot welding. The mechanical joining processes were simple with ease of maintenance, however, the use of steel components correlated with heightened corrosion rates and higher resistivity. Spot welding joints tended to produce low joining strength due to the brittleness of the welding spot. Nonetheless, the spot weld joints demonstrated minimal changes in resistivity following corrosion exposure as opposed to the mechanical joining counterparts.
References
R. Frank and C. Morton, Comparative corrosion and current burst testing of copper and aluminum electrical power connectors, Fourtieth IAS Annual Meeting Conference, Proceeding, 2005, 442-447.
H. Moslemi, K. Farhangdoost and P. Zamani, Fatigue life evaluation of single and two riveted coach peel joints using strain-life criteria, AUT Journal of Mechanical Engineering, 2019, 3(2), 229-234.
C. Lei, Q. Huang and Y. Bi, Tensile load distribution improvement of three-row riveted lap joint based on different squeezing displacement combinations, Coatings, 2021, 11, 856.
T. Bothiraj and M. Saravanan, Experimental investigation of friction stir blind riveting process for similar and dissimilar alloy sheet, Journal of Advanced Mechanical Design Systems and Manufacturing, 2018, 12(1), 17-00679.
D.C. Saha, and Y.D. Park, A review on Al-Al/Al-steel resistance spot welding technologies for light weight vehicles, Journal of Welding and Joining, 2011, 29(4), 35-40.
Y. Yang, Y. Li, J. Bi, H. Liu, S. Ao and Z. Luo, Study on the corrosion behavior of resistance spot welded dissimilar 2195/5A06 joints, Journal of Materials Engineering and Performance, 2023, 32(7), 3114-3128.
AZO Materials, Aluminium Alloys - Aluminium 1050 Properties, Fabrication and Applications, 2005. https://www.azom.com/article.aspx?ArticleID=2798 (Accessed on 30 January 2024)
P. Saowapa, S. Wichachai, R. Munprom and R. Techapiesancharoenkij, Study the spot welding for difference material between copper C1100 and aluminum A1050, CRU-National Conference in Science and Technology: NCST 6th, Proceeding, 2023.
ASTM E8/E8M-13a, Standard Test Methods for Tension Testing of Metallic Materials ,2015.
K.O Cooke and T.I. Khan, Microstructure development during low-current resistance spot welding of aluminum to magnesium, Journal of Manufacturing and Materials Processing, 2019, 46-48.
A. Groysman, Corrosion for everybody, Springer Science and Business Media, 2019.
M.F. Ibrahim, Effect of different sodium chloride (NaCl) concentration on corrosion of coated steel, Doctoral Dissertation, University Malaysia Pahang, Malaysia, 2013.
F. Brownlie, T. Hodgkiess, A. Pearson and A. Galloway, Electrochemical evaluation of the effect of different NaCl concentrations on low alloy-and stainless steels under corrosion and erosion-corrosion conditions, Corrosion and Materials Degradation, 2022, 3, 101-126.
R.S. Waremra and P. Betaubun, Analysis of electrical properties using the four point probe method, E3S Web of Conferences, EDP Sciences, 2018, 73, 13019.
V. Tsakiris, W. Kappel, and G. Alecu, Solid state diffusion welding of Cu-Fe/Al/Ag and Al-Ni dissimilar metals, Journal of Optoelectronics and Advanced Materials, 2011, 13(9), 1176.
A.M. Helmenstine, A table of electrical conductivity and resistivity of common materials, ThoughtCo, 2019. https://www.thoughtco.com/table-of-electrical-resisitivity-conductivity-608499. (Accessed on 30 September 2023)
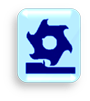
Downloads
Published
Issue
Section
License
Copyright (c) 2024 http://j.cit.kmutnb.ac.th/th/

This work is licensed under a Creative Commons Attribution-NonCommercial-NoDerivatives 4.0 International License.
ผลงานวิจัยและบทความวิชาการที่ปรากฏในวารสารนี้ เป็นความคิดเห็นอิสระของผู้เขียน ผู้เขียนจะต้องเป็นผู้รับผิดชอบต่อผลทางกฎหมายใด ๆ ที่อาจจะเกิดขึ้นจากบทความนั้น กองบรรณาธิการและคณะจัดทำวารสารฯไม่จำเป็นต้องเห็นด้วยเสมอไป