Real-time Feedback Control for Uniform Weld Bead using Adaptive PID Controller with Infrared Image Processing in Fiber Laser Welding of Low Carbon Steel
DOI: 10.14416/j.ind.tech.2023.12.003
Keywords:
Laser welding, Feedback control, Image processing, Low carbon steel sheetAbstract
Fiber laser has considerable advantages; that is, high melting efficiency, high power, and power density. However, during the welding process, if the thickness of the steel sheet is not stable or the process has a defect, this could affect the control. To make the continuity in welds, the research is intended to propose a quality control system for the real-time weld beads. The process involves the welding of the low-carbon steel sheet by laser fiber of varying thicknesses of 0.5 to 1.0 mm. The infrared image processing is used to determine the molten pool during the welding process. Then, this data is input to the adaptive PID feedback control system in order to control the width of the weld bead quality (Uniform Weld Bead). In this regard, the width of the molten pool is used as the main input parameter for controlling the power of the fiber laser in accordance with the steel sheet thickness. The research results indicate that the adaptive PID can control the power of the fiber laser so that the molten pool width is maintained within ±1.0 mm. accuracy from the setting point. Moreover, the experiment shows that the weld beads have full penetration and continuity. The standard deviations of the thickness adjustment in the 0.5-1.0 mm. and 1.0-0.5 mm directions are 0.22 and 0.23 respectively. Therefore, the feedback control technique is appropriate for the automatic laser welding of the worksheets with a thickness of 0.5-1.0 mm.
References
D.Y. You, X.D Gao and S. Katayama, Review of laser welding monitoring, Science and Technology of Welding and Joining, 2014, 19(3), 181-201.
J. Stavridis, A. Papacharalampopoulos and P. Stavropoulos, Quality assessment in laser welding: a critical review. The International Journal of Advanced Manufacturing Technology, 2018, 94, 1825-1847.
W. Huang, and R. Kovacevic, Feasibility study of using acoustic signals for online monitoring of the depth of weld in the laser welding of high-strength steels. Proceedings of the Institution of Mechanical Engineers, Part B: Journal of Engineering Manufacture, 2009, 223(4), 343-361.
W. Meng, X. Yin, J. Fang, L. Guo, Q. Ma and Z. Li, Dynamic features of plasma plume and molten pool in laser lap welding based on image monitoring and processing techniques, Optics and Laser Technology, 2019, 109, 168-177.
A.R. Konuk, R.G. Aarts, A.J. Huis, T. Sibillano, D. Rizzi and A. Ancona, Process control of stainless steel laser welding using an optical spectroscopic sensor, Physics Procedia, 2011, 12, 744-751.
M. Xia, E. Biro, Z. Tian and Y.N. Zhou, Effects of heat input and martensite on HAZ softening in laser welding of dual phase steels, ISIJ international, 2008, 48(6), 809-814.
M. Xia, Z. Tian, L. Zhao, and Y.N. Zhou, Fusion zone microstructure evolution of Al-alloyed TRIP steel in diode laser welding, Materials transactions, 2008, 49(4), 746-753.
Z. Gu, S. Yu, L. Han, X. Li, and H. Xu, Influence of welding speed on microstructures and properties of ultra-high strength steel sheets in laser welding, ISIJ international, 2012, 52(3), 483-487.
M. Kushwah, and A. Patra, PID controller tuning using Ziegler-Nichols method for speed control of DC motor, International Journal of Scientific Engineering and Technology Research, 2014, 3(13), 2924-2929.
B. Kaewprachum, and P. Srisungsitthisunti, Real-time process monitoring of laser welding by infrared camera and image processing, Key Engineering Materials, 2020, 856, 160-168.
Y.W. Huang, P.C. Tung and C.Y. Wu, Tuning PID control of an automatic arc welding system using a SMAW process, The International Journal of Advanced Manufacturing Technology, 2007, 34, 56-61.
W. Mao, S. Li, P. Liu and J. Xue, Study on double-pulse welding process of aluminum alloy based on fuzzy self-tuning of PID parameters, 12th International Conference on Intelligent Human-Machine Systems and Cybernetics (IHMSC), Proceeding, 2020, 1, 167-170.
A. Božič, M. Kos and M. Jezeršek, Power control during remote laser welding using a convolutional neural network, Sensors, 2020, 20(22), 6658.
G. Peng, B. Chang, G. Wang, Y.Gao, R. Hou, S. Wang and D. Du, Vision sensing and feedback control of weld penetration in helium arc welding process, Journal of Manufacturing Processes, 2021, 72, 168-178.
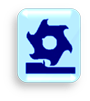
Downloads
Published
Issue
Section
License

This work is licensed under a Creative Commons Attribution-NonCommercial-NoDerivatives 4.0 International License.
ผลงานวิจัยและบทความวิชาการที่ปรากฏในวารสารนี้ เป็นความคิดเห็นอิสระของผู้เขียน ผู้เขียนจะต้องเป็นผู้รับผิดชอบต่อผลทางกฎหมายใด ๆ ที่อาจจะเกิดขึ้นจากบทความนั้น กองบรรณาธิการและคณะจัดทำวารสารฯไม่จำเป็นต้องเห็นด้วยเสมอไป