Effects of Pin-perforation Shape on Thermal Enhancement Factor of Pin-fin Heat Sink via Numerical Simulation
DOI: 10.14416/j.ind.tech.2023.03.002
Keywords:
Circular pin-fin heat sink, Nusselt number, Pressure drop, Thermal enhancement factorAbstract
Effects of pin-perforation shape on the thermal enhancement factor of pin-fin heat sink via numerical simulation are presented here in this study. The material for the pin-fin heat sink is assigned to be an aluminum alloy, and the shape of the pin fins on the heat sink is circular. The heat source generating 45 W of heat flux is placed on the bottom of the heat sink. The inlet air temperature and velocity are 300 K and 5.2 m/s, respectively. The numerical air-flow model of steady turbulent main flow follows the standard k – ε. Four pin-perforation shapes on pin fins are diamond, triangular, hexagonal, and circular of which all share the same ratio of the air/heat-sink interfacial surface area (ISA) to the total volume of the heat sink (TVH) of approximately 0.54 mm-1. The lowest to highest Nusselt number (Nu), which represents the convective heat transfer efficiency, is found in diamond-perforation, triangular-perforation, hexagonal-perforation, and circular-perforation pin-fin heat sink, respectively. The lowest to highest pressure drop (ΔP), which signifies the hydraulic friction loss due to airflow restriction caused by pin-fin heat sinks, is found in circular-perforation, hexagonal-perforation, diamond-perforation, and triangular-perforation pin-fin heat sink, respectively. Lastly, the thermal enhancement factor (TEF), a ratio of the convective heat transfer efficiency to friction loss, from the lowest to highest are diamond-perforation, triangular-perforation, hexagonal-perforation, and circular-perforation pin-fin heat sinks, respectively. The circular-perforation pin-fin heat sink is shown to yield the highest TEF which is 43.1% higher than that of the pin-fin heat sink without pin-perforation.
References
K. Altaf, A. Tariq, S.W. Ahmad, G. Hussain, T.A.H. Ratlamwala and H.M. Ali, Thermal and hydraulic analysis of slotted plate fins heat sinks using numerical and experimental techniques, Case Studies in Thermal Engineering, 2022, 35, 102109.
K. Nilpueng, H.S. Ahn, D.W. Jerng and S. Wongwises, Heat transfer and flow characteristics of sinusoidal wavy plate fin heat sink with and without crosscut flow control, International Journal of Heat and Mass Transfer, 2019, 137, 565-572.
M.A.H. Abdelmohimen, K. Almutairi, M.A. Elkotb, H.E. Abdelrahman and S. Algarni, Numerical investigation of using different arrangement of fin slides on the plate-fin heat sink performance, Thermal Science, 2021, 25(6B), 4683-4693.
E.C. Silva, Á.M. Sampaio and A.J. Pontes, Evaluation of active heat sinks design under forced convection-effect of geometric and boundary parameters, Materials, 2021, 14, 2041.
D. Soodphakdee, M. Behnia and D.W. Copeland, A comparison of fin geometries for heatsinks in laminar forced convection: part i – round, elliptical, and plate fins in staggered and in-line configurations, The International Journal of Microcircuits and Electronic Packaging, 2001, 24(1), 68-76.
E.H. Muhammad, A comparison of the heat transfer performance of a hexagonal pin fin with other types of pin fin heat sinks, International Journal of Science and Research, 2015, 4(9), 1781-1789.
K. Bilen, U. Akyol and S. Yapici, Heat transfer and friction correlations and thermal performance analysis for a finned surface, Energy Conversion and Management, 2001, 42(9), 1071-1083.
O.N. Şara, Performance analysis of rectangular ducts with staggered square pin fins, Energy Conversion and Management, 2003, 44(11), 1787-1803.
P. Naphon and A. Sookkasem, Investigation on heat transfer characteristics of tapered cylinder pin fin heat sinks, Energy Conversion and Management, 2007, 48(10), 2671-2679.
B. Sahin and A. Demir, Thermal performance analysis and optimum design parameters of heat exchanger having perforated pin fins, Energy conversion and management, 2008, 49(6), 1684-1695.
B. Sahin and A. Demir, Performance analysis of a heat exchanger having perforated square fins, Applied Thermal Engineering, 2008, 28(5-6), 621-632.
M. Baruah, A. Dewan and P. Mahanta, Performance of elliptical pin fin heat exchanger with three elliptical perforations, CFD Letters, 2011, 3(2), 65-73.
A. Al-Damook, N. Kapur, J.L. Summers and H.M. Thompson, An experimental and computational investigation of thermal air flows through perforated pin heat sinks, Applied thermal engineering, 2015, 89, 365-376.
A. Al-Damook, J.L. Summers, N. Kapur and H. Thompson, Effect of temperature-dependent air properties on the accuracy of numerical simulations of thermal airflows over pinned heat sinks, International Communications in Heat and Mass Transfer, 2016, 78, 163-167.
V.V. Dhole, V.S. Shinde and S.S. Kore, Thermal and hydraulic performance analysis of cylindrical pin fin heat sink with conical perforations, International Journal of Current Engineering and Technology, 2016, 5, 436-440.
W. Al-Sallami, A. Al-Damook and H.M. Thompson, A numerical investigation of thermal airflows over strip fin heat sinks, International Communications in Heat and Mass Transfer, 2016, 75, 183-191.
C.H. Wu, H.W. Tang and Y.T. Yang, Numerical simulation and optimization of turbulent flows through perforated circular pin fin heat sinks, Numerical Heat Transfer, Part A: Applications, 2017, 71(2), 172-188.
A.S. Tijani and N.B. Jaffri, Thermal analysis of perforated pin-fins heat sink under forced convection condition, Procedia Manufacturing, 2018, 24, 290-298.
M. Hatem, H. Abdellatif and W. Hussein, Enhancement of perforated pin-fins heat sink under forced convection, International Research Journal of Engineering and Technology, 2020, 7(10), 1440-1445.
N.A. Ghyadh, S.S Ahmed and M.A.R.S. Al-Baghdadi, Enhancement of forced convection heat transfer from cylindrical perforated fins heat sink-CFD study, Journal of Mechanical Engineering Research and Developments, 2021, 44(3), 407-419.
S.S. Kore, R. Yadav, S. Chinchanikar, P. Tipole and V. Dhole, Experimental investigations of conical perforations on the thermal performance of cylindrical pin fin heat sink, International Journal of Ambient Energy, 2022, 43(1), 3431-3442.
S.B. Chin, J.J. Foo, Y.L. Lai and T.K.K. Yong, Forced convective heat transfer enhancement with perforated pin fins, Heat and Mass Transfer, 2013, 49, 1447-1458.
C.H. Huang, Y.C. Liu and H. Ay, The design of optimum perforation diameters for pin fin array for heat transfer enhancement, International Journal of Heat and Mass Transfer, 2015, 84, 752-765.
C.H. Huang and M.H. Chen, An estimation of the optimum shape and perforation diameters for pin fin arrays, International Journal of Heat and Mass Transfer, 2019, 131, 72-84.
Y.T. Yang and H.S. Peng, Numerical study of the heat sink with un-uniform fin width designs, International Journal of Heat and Mass Transfer, 2009, 52(15-16), 3473-3480.
A. Boonloi and W. Jedsadaratanachai, Numerical investigation on turbulent forced convection and heat transfer characteristic in a square channel with discrete combined V-baffle and V-orifice, Case Studies in Thermal Engineering, 2016, 8, 226-235.
A. Boonloi and W. Jedsadaratanachai, Numerical study on flow and heat transfer mechanisms in the heat exchanger channel with V-orifice at various blockage ratios, gap spacing ratios, and flow directions, Modelling and Simulation in Engineering, 2019, 2019, 8656435.
A. Boonloi and W. Jedsadaratanachai, CFD analysis on heat transfer characteristics and fluid flow structure in a square duct with modified wavy baffles, Case Studies in Thermal Engineering, 2022, 29, 101660.
A. Al-Damook, N. Kapur, J.L. Summers and H.M. Thompson, Computational design and optimisation of pin fin heat sinks with rectangular perforations, Applied Thermal Engineering, 2016, 105, 691-703.
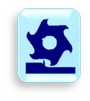
Downloads
Published
Issue
Section
License

This work is licensed under a Creative Commons Attribution-NonCommercial-NoDerivatives 4.0 International License.
ผลงานวิจัยและบทความวิชาการที่ปรากฏในวารสารนี้ เป็นความคิดเห็นอิสระของผู้เขียน ผู้เขียนจะต้องเป็นผู้รับผิดชอบต่อผลทางกฎหมายใด ๆ ที่อาจจะเกิดขึ้นจากบทความนั้น กองบรรณาธิการและคณะจัดทำวารสารฯไม่จำเป็นต้องเห็นด้วยเสมอไป