Effect of Crosslinking Agent and Blowing Agent on the Properties of Natural rubber: Morphology and Mechanical Properties - Before and After Fuel Swelling
DOI: 10.14416/j.ind.tech.2021.12.003
Keywords:
Natural rubber, Swelling, Crosslinking agent, Blowing agent, PorousAbstract
This research work studies the effect of crosslinking agent and blowing agent at various concentrations, on morphology and mechanical properties, as before and after fuel swelling, of the natural rubbers which applied as the self-sealing layer of the fuel tank. The rubbers were blended with the crosslinking agent (0.5 and 1.5 phr), and the blowing agent (0, 4, 8 and 12 phr) at various concentrations, by using a two-roll mill machine. The curing time (tc90) of each rubber was measured by using an oscillating disk rheometer. The rubbers were fabricated by using a hot-press compression molding machine. Then, the rubbers were measured the porous content and the mechanical properties (such as ultimate tensile strength, elongation at break and modulus), as before and after fuel swelling, by using an optical microscope and a universal testing machine, respectively. It was found that the crosslinking agent and the blowing agent affected to morphology and mechanical properties of the rubbers, as before and after fuel swelling. From these results, it can be concluded that the best formula that proper to use as self-sealing materials was NR2, which was the rubber that blended with the crosslinking agent and the blowing agent at 1.5 and 4 phr, respectively. Because this rubber has a proper ratio of the rubber matrix and the porous, as a result, it has the highest rate of swelling and strength, as before and after fuel swelling.
References
[2] P.J. Dasher, Self-sealing fuel tank, United State Patent, US41778741A.
[3] T.S. Ohnstad, R.A. Monk, Sealing-reaction, layer-effective, stealth liner for synthetic fuel container, United States Patent Application, US2009/0050629 A1.
[4] L. Spenadel, Synthetic rubber for self-sealing fuel tanks, Applied Science Research Laboratory, 1959, 51(8), 935-936.
[5] www.atlltd.com/industries/defence-security/self-sealing-tanks. (Accessed on 14 February 2020)
[6] R.A.Crawford, Self-sealing fuel tank construction, United State Patent, US47784843A.
[7] www.hutchinsoninc.com/protected-fuel-tank/. (Accessed on 11 January 2020)
[8] C.C. Chin, N.D.L. Musbah, I. Abdullah and A.M. Lazim, Characterization and evaluation of prudent liquid natural rubber-based foam for oil spill control application, Arabian Journal for Science and Engineering, 2018, 43, 6097–6108.
[9] www.dsiac.org/articles/advances-in-self-sealing-fuel-tank-technology/. (Accessed on 25 January 2020)
[10] M. Barlkani and C. Hepburn, Determination of crosslink density by swelling in the castable polyurethane elastomer based on 1/4-cyclohexane diisocyanate and para-phenylene diisocyanate. Iranian Journal of Polymer Science and Technology, 1992, 1(1), 1–5.
[11] A. Khalaf, A. Yehia, M. Ismail and H. El-Sabbagh, High performance oil resistant rubber, Open Journal of Organic Polymer Materials, 2012, 2(04), 88-93.
[12] R. Maharsia, N. Gupta and H.D. Jerro, Investigation of flexural strength properties of rubber and nanoclay reinforced hybrid syntactic foams, Materials Science and Engineering: A, 2006, 417(1), 249-258.
[13] O. Okay, S. Durmaz and B. Erman, Solution cross-linked poly (isobutylene) gels: synthesis and swelling behavior, Macromolecules, 2000, 33(13), 4822-4827.
[14] L.J. Gibson, Biomechanics of cellular solids, Journal of Biomechanics, 2005, 38(3), 377-399.
[15] M. Krumova, D. Lopez, R. Benavente, C. Mijangos and J. Perena, Effect of crosslinking on the mechanical and thermal properties of poly (vinyl alcohol). Polymer, 2000, 41(26), 9265-9272.
[16] J. He, Z. Zhang, H. Kristiansen, K. Redford, G. Fonnum and G. Modahl, Crosslinking effect on the deformation and fracture of monodisperse polystyrene-co-divinylbenzene particles. Express Polymer Letters, 2013, 7(4), 365-374.
[17] G.R. Hamed, Materials and compounds, Engineering with Rubber: How to Design Rubber Components, 3rd Ed., Hanser Books, OH, USA, 1992.
[18] J. Bras, M.L. Hassan, C. Bruzesse, E.A. Hassan, N.A. El-Wakil and A. Dufresne, Mechanical, barrier, and biodegradability properties of bagasse cellulose whiskers reinforced natural rubber nanocomposites, Industrial Crops and Products, 2010, 32(3), 627-633.
[19] H. Ismail, H.D. Rozman, R.M. Jaffri and Z.A.M. Ishak, Oil palm wood flour reinforced epoxidized natural rubber composites: the effect of filler content and size. European Polymer Journal, 1997, 33(10), 1627-1632.
[20] D. Ceylan, S. Dogu, B. Karacik, S. D. Yakan, O. S. Okay and O. Okay, Evaluation of butyl rubber as sorbent material for the removal of oil and polycyclic aromatic hydrocarbons from seawater, Environmental Science and Technology, 2009, 43(10), 3846-3852.
[21] H. Li, L. Liu, F. Yang, Hydrophobic modification of polyurethane foam for oil spill cleanup. Marine Pollution Bulletin, 2012, 64(8), 1648-1653.
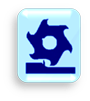