Bi-objective Design Optimization of a Manipulator Arm
DOI: 10.14416/j.ind.tech.2021.12.006
Keywords:
Bi-objective design optimization, Manipulator Arm, Design of experimentsAbstract
Global business competition forces case study companies to improve their manipulator arms by providing better quality and lower costs to increase their domestic and international competitiveness. The authors investigated a manipulator arm design case study problem for loading 75 kilograms, with 15 kilograms mounted on the back as a counterbalance. The designer can adjust the size of each part while maintaining the original overall shape of the manipulator arm. The case study company determines the factors and the possible level of improvements in size, allowing it to either purchase or manufacture the part in Thailand. This paper proposes a bi-objective design optimization method for a manipulator arm by applying the finite element method with a full factorial design of experiment and optimization to minimize the total production cost and maximize safety factors. Results showed that the proposed method can reduce the total production cost from THB 34,117.64 to THB 25,698.40, while the factor of safety value increases from 3.08 to 9.13, compared to the traditional mechanical arm design.
References
[2] S. Mahalingam and A. Sharan, The optimal balancing of the robotic manipulators, IEEE International Conference on Robotics and Automation, Proceeding, 1986, 828-835.
[3] W.S. Newman and N. Hogan, Time optimal control of balanced manipulators, Journal of Dynamic Systems, Measurement, and Control, 1989, 111(2), 187–193.
[4] C.A.C. Coello, A.D. Christiansen, and A.H. Aguirre, Multiobjective design optimization of counterweight balancing of a robot arm using genetic algorithms, the 7th IEEE International Conference on Tools with Artificial Intelligence, Proceeding, 1995, 20-23.
[5] C. Baradat, V. Arakelian, S. Briot, and S. Guegan, Design and prototyping of a new balancing mechanism for spatial parallel manipulators, Journal of Mechanical Design, Transactions of the ASME, 2008, 130(7), 0723051-07230513.
[6] A. Nikoobin and M. Moradi, Optimal balancing of robot manipulators in point-to-point motion, Robotica, 2011, 29(2), 233-244.
[7] W. Xu, D. Meng, H. Liu, X. Wang, and B. Liang, Singularity-free trajectory planning of free-floating multiarm space robots for keeping the base inertially stabilized, IEEE Transactions on Systems, Man, and Cybernetics: Systems, 2019, 49(12), 2464- 2477.
[8] J. Wang and X. Kong, An optimization method for the static balancing of manipulators using springs, the 44th Mechanisms and Robotics Conference, Proceeding, 2020, 22217.
[9] M.H. Ali, Y. Kuralbay, A. Aitmaganbet, and M.A.S. Kamal, Design of a 6-DOF robot manipulator for 3D printed construction, Materials Today: Proceedings, In Press, 31 July 2021.
[10] R. Xu, J. Luo, and M. Wang, Optimal grasping pose for dual-arm space robot cooperative manipulation based on global manipulability, Acta Astronautica, 2021, 183, 300-309.
[11] D. Cholaseuk, Optimum and robust geometric design of mechanical parts, Thesis, Columbia University, USA, 2001.
[12] D. Cholaseuk, A stress-based material distribution method for optimum shape design of mechanical parts, Thammasat International Journal of Science and Technology, 2006, 11(3), 17-21.
[13] A. Manee-ngam, P. Saisirirat, and P. Suwankan, Hook design loading by the optimization method with weighted factors rating method, Energy Procedia, 2017, 138, 337–342.
[14] T. Kot, Z. Bobovský, M. Brandstötter, V. Krys, I. Virgala, and P. Novák, Finding optimal manipulator arm shapes to avoid collisions in a static environment, Applied Sciences (Switzerland), 2021, 11(1), 64.
[15] https://drive.google.com/file/d/1NpY0PhR gTiJzeCKOaKCcApZq7PCW32S2/view?usp=sharing (Accessed on 14 October 2021)
[16] www.syssteel.com/wp-content/uploads/2018/09/AW-Catalog-Thai-Effective-April-2018.pdf. (Accessed on 14 October 2021)
[17] www.meadinfo.org/2010/09/jis-g-3101-ss400-steel-properties-spec.html. (Accessed on 14 October 2021)
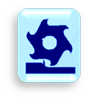