Applying the Lean Concept to Improve the Oil Pipelines Processing for Tractor: A Case Study of ABC Company Ltd.
DOI: 10.14416/j.ind.tech.2021.10.002
Keywords:
Production Process, Cycle Time, Galvanizing ProcessAbstract
The objectives of this research were (1) to study the working processes (2) to increase the efficiency of the oil pipeline parts manufacturing processes and (3) to reduce the amount of waste generated. The company has problems with the oil pipeline parts rusting and requires an increase in the speed of the processes of producing oil pipeline parts. The causes of the problems will be analyzed using brainstorming, Why Why Analysis. Then the working method was improved by applying the Lean concept, which is a system to eliminate wastage and improve quality by applying ECRS principles. The production line was balanced, to improve the problems that arose. After the improvement of the rust problems by coating the workpieces with galvanization, it was found that the original 20.00% of work that was wasted was removed completely – a 100% improvement. Also, after improving the production processes of oil pipeline parts, it was found that the production cycle was reduced from 89.13 to 51.61 seconds per item. The production cycle time was reduced by 42.10% and the total production time was reduced from 289.33 to 177.14 seconds per item, reduced to 38.78%. Also, the number of employees required was reduced from the original 6 people to only 4 people. Finally, the workflow sub-steps were reduced from the original 26 sub-steps to 18 sub-steps, representing a 30.77% reduction.
References
[2] R. Musikapong, Application of value stream mapping to improve the production process in plastic film industry: A case study of TPK company, Thesis, Burapha University, Thailand, 2015. (in Thai)
[3] S. Vanhaku, Line balancing of 4 heads 2 platters head disk head assembly line, Thesis, Thailand, 2015. (in Thai)
[4] R. Kanjanapanyakom, Industrial work study, Top Publishing Co., Ltd., Bangkok, Thailand, 2009. (in Thai).
[5] J. Santos, R. Wysk and J.M. Torres, Improving production with lean thinking. John Wiley & Sons, Inc., NY, USA, 2015.
[6] S. Panthong and B. Phruksaphanrat, Process improvement and line balancing for heat pipe production line by computer simulation, Thesis, Thammasat University, Thailand, 2020. (in Thai)
[7] P. Pukasorn and S. Sriaram, Efficiency increase in a production process of wooden furniture a case study: Indexinterfern company limited, Thesis, King Mongut’s University of Technology North Bangkok, Thailand, 2012. (in Thai)
[8] T. Sunarak, Production line effciency improvement: A case of stator D frame model production line, Thesis, Mahanakorn University of Technology, Thailand, 2012. (in Thai)
[9] S. Ketsarapong, Defect reduction in process of motorcycle exhaust parts, Thesis, Kasetsart University Si Racha Campus, Thailand, 2012. (in Thai).
[10] N.Jivapaisarnpong, Efficiency improvement in supply chain operation of plastic packaging factory, Thesis, Dhurakij Pundit University, Thailand, 2012. (in Thai)
[11] P. Ardparu, Loss reduction in circuit breaker factory, Thesis, Chulalongkorn University, Thailand, 2008. (in Thai)
[12] R. Pongsuwan, Efficiency improvement work in process applying of production, the principle of ECRS case study in P.C. Takashima Co., LTD., Thesis, Rajabhat Rajanagarindra University, Thailand, 2018. (in Thai)
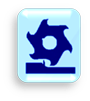