Consideration of the Optimizing Condition in Welding Hardfacing on Wear Resistance with Hot-Wire Gas Tungsten Arc Welding Process by Response Surface Methodology
DOI: 10.14416/j.ind.tech.2021.08.003
Keywords:
Optimization, Hot wire, Response Surface MethodologyAbstract
Response Surface Methodology (RSM) was used to determine optimum condition for welding hardfacing. Box-Behnken experimental design was applied to optimize the welding current, hot wire current and welding speed on wear resistant of weld. The results showed that these three factors affected on wear rate of welding hardfacing. The obtained experimental data were suitable for the quadratic equation because it showed high coefficient of determination (97.80 %). The 3D response surface plot and the contour plot derived from the mathematical models were applied to determine the optimal condition. The optimum welding condition were follows: welding current 200.505 amp, hot wire current 180 amp, and welding speed 80 mm/min, the wear rate lower of weld was 3.4366 mm3. The optimization and experiment results were then compared. The results of the comparison showed a good correspondence.
References
[2] Y.S. Tarng, S.C Juang and C.H. Chang, The use of grey-based Taguchi methods to determine submerged arc welding process parameters in hardfacing, Journal of materials processing technology, 2002, 128(1-3), 1-6.
[3] V.Balasubramanian, R . Varahamoorthy, C. S Ramachandran and C. Muralidharan, Selection of welding process for hardfacing on carbon steels based on quantitative and qualitative factors, The International Journal of Advanced Manufacturing Technology, 2009, 40, 887-897.
[4] G.R.C. Pradeep, A. Ramesh and B.D. Prasad, A review paper on hardfacing processes and materials, International Journal of Engineering Science and Technology, 2010, 2(11), 6507-6510.
[5] J.J. Coronado, H.F. Caicedo and A.L. Gómez, The effects of welding processes on abrasive wear resistance for hardfacing deposits. Tribology International, 2019, 42(5), 745-749.
[6] S.H. Kim and Y.S. Kim, Effect of ductility on dry sliding wear of medium carbon steel under low load conditions, Metals and Materials, 1999, 5(3), 267-271.
[7] A.P. Modi, Effects of microstructure and experimental parameters on high stress abrasive wear behaviour of a 0.19 wt% C dual phase steel, Tribology International, 2007, 40(3), 490-497.
[8] M.R. Chen, S.J. Lin, J.W. Yeh, M.H. Chuang, S.K. Chen and Y.S. Huang, Effect of vanadium addition on the microstructure, hardness, and wear resistance of Al 0.5 CoCrCuFeNi high-entropy alloy, Metallurgical and Materials Transactions A, 2006. 37(5), 1363-1369.
[9] M. Sadeghian, M. Shamanian and A. Shafyei, Effect of heat input on microstructure and mechanical properties of dissimilar joints between super duplex stainless steel and high strength low alloy steel, Materials & Design, 2014, 60, 678-684.
[10] H. Dong, X. Hao and D. Deng, Effect of welding heat input on microstructure and mechanical properties of HSLA steel joint, Metallography, microstructure, and analysis, 2014, 3(2), 138-146.
[11] H. Vashishtha, R.V. Taiwade, S. Sharma and A.P. Patil, Effect of welding processes on microstructural and mechanical properties of dissimilar weldments between conventional austenitic and high nitrogen austenitic stainless steels, Journal of Manufacturing Processes, 2017, 25, 49-59.
[12] F. Wang, S. Williams, P. Colegrove and A. Antonysamy, Microstructure and mechanical properties of wire and arc additive manufactured Ti-6Al-4V, Metallurgical and materials transactions A, 2003, 44(2), 968-977.
[13] F. Schreiber, B. Allebrodt and T. Erpel, Hardfacing material solutions for high performance coatings in wear and corrosion applications. Zavarivanje i zavarene konstrukcije, 2019, 64(1), 11-21.
[14] S. Gao, H. Nakashin, M. Yamamoto, K. Shinozaki, K. Kadoi, H. Watanabe, and G. AP, Development of WC hard-facing welding process using pulse heated hot-wire gas tungsten arc welding system, Quarterly Journal of the Japan Welding Society, 2013, 31(4), 57s-60s.
[15] H. He, C. Wu, S. Lin and C. Yang, Pulsed TIG welding–brazing of aluminum–stainless steel with an Al-Cu twin hot wire, Journal of Materials Engineering and Performance, 2019, 28(2), 1180-1189.
[16] S.K. Shihab, Optimization of WEDM process parameters for machining of friction-stir- welded 5754 aluminum alloy using Box–Behnken design of RSM, Arabian Journal for Science and Engineering, 2018, 43(9), 5017-5027.
[17] M. Ragavendran, N. Chandrasekhar, R. Ravikumar, R. Saxena, M. Vasudevan and A.K. Bhaduri, Optimization of hybrid laser–TIG welding of 316LN steel using response surface methodology (RSM), Optics and Lasers in Engineering, 2017, 94, 27-36.
[18] N. Kiaee and M.A Khafri, Optimization of gas tungsten arc welding process by response surface methodology, Materials and Design (2014), 54, 25-31.
[19] S.T. Selvamani, S. Divagar and M. Vigneshwar, Application of response surface methodology (RSM) in friction welding AISI 1020 grade steel joints, International Journal of Engineering Research in Africa, 2015, 16, 38-44.
[20] S. Srivastava and R.K. Garg, Process parameter optimization of gas metal arc welding on IS:2062 mild steel using response surface methodology, Journal of Manufacturing Processes, 2017,25, 296-305.
[21] P.M. Ajith, T.A. Husain, P. Sathiya and S. Aravindan, Multi-objective optimization of continuous drive friction welding process parameters using response surface methodology with intelligent optimization algorithm, Journal of Iron and Steel Research, International, 2015, 22(10), 954-960.
[22] R. Paventhan, P.R. Lakshminarayanan and V. Balasubramanian, Prediction and optimization of friction welding parameters for joining aluminium alloy and stainless steel, Transactions of Nonferrous Metals Society of China, 2011, 21(7), 1480-1485.
[23] S. Prasomthong and S. Namkaew, The influence of adding aluminum welding wire onm Properties and chemical composition of the welding hardfacing welded low carbon steel by gas tungsten arc welding process, The Journal of Industrial Technology, 2019, 15(1), 27-36. (in Thai)
[24] K. Hinkelmann and O. Kempthorne, Design and analysis of experiments, Volume 1: Introduction to experimental design 1st ED., John Wiley and Sons, Inc., NY, USA, 1994.
[25] I. Worapun, C. Chooppava and C. Thinvongpituk, Optimal conditions of friction welding process for AISI 1015 steel using response surface methodology, Asia-Pacific Journal of Science and Technology, 2013, 18(6), 909-924. (in Thai)
[26] S. Ayadi and A. Hadji, Effect of Chemical composition and heat treatments on the microstructure and wear behavior of manganese steel, International Journal of Metal casting, (2021), 15: 510-519.
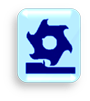