A Study of Factors for Chemical Cost Reduction in the Brake Pad Manufacturing Process
DOI: 10.14416/j.ind.tech.2021.03.002
Keywords:
Brake Pad, Tolerances, 2k Full Factorial Design, 3k Full Factorial DesignAbstract
The case study company had a surplus chemical powder from brake pad manufacturing processes at 180,000 kilograms per year or 15.84% of all chemical powder in manufacturing processes and was resulting in high manufacturing cost. The cost of a surplus chemical powder was about 13 million baht per year. The objective of this research was to find the cause and reduced a surplus chemical powder from brake pad manufacturing processes. Brainstorming of case study company experts found the cause of a surplus chemical powder in brake pad manufacturing from necessary tolerance weight of chemical powder in the production so that no problem in production: 1) variation of thickness in grinding process 2) variation of thickness in hot press process and 3) variation of slotting process and chamfering process. After that break pad thickness variation problem was analyzed preliminary affect factor by Why-Why Analysis. And factors were analyzed to decide which factors affected the problem by 2k Full Factorial Design experiment. The factors that were obtained were then tested in 3k Full Factorial Design to find the optimal levels of various factors. In conclusion, the optimum level of each factor from the experiment can be reduced chemical powders by 8.75% in the brake pads production and can be reduced cost by 2.60% in brake pad manufacturing processes.
References
[2] P. Boonkliang, Variation reduction of acrylic foam tape width in slitting process by six sigma approach, Thesis, Chulalongkorn University, Thailand. 2009, pp. 130-138. (in Thai)
[3] M. Sae-ung, A study of factors affecting plating thickness in electro-plating Process, Thesis, Chulalongkorn University, Thailand. 2001, pp. 62-107. (in Thai)
[4] W. Thaweesuk, The study of factors effecting the crown inducement of write/read head assembly of hard disk drive by using the design of experiment, Thesis, Chulalongkorn University, Thailand. 2003, pp. 84-101. (in Thai)
[5] P. Natasan, Design of experiment for analyzing factors in corrugated box production process, Thesis, Chulalongkorn University, Thailand. 2010, pp. 93-159. (in Thai)
[6] W. Hemso, Defect reduction from brake pads production by using DMAIC method, Thesis, Rajamangala University of Technology Thanyaburi, Thailand. 2013, pp. 97-173. (in Thai)
[7] P. Parakawong na ayuthaya, Design of experiment to waste reduction injection process of electronic parts, Thesis, Silpakorn University, Thailand. 2018, pp. 15-21, 77-88. (in Thai)
[8] http://leanmanufacturing-tawatchai.blogspot. com/2009/12/why-why-analysis-5-gen.html (Accessed on 10 August 2019)
[9] https://www.sasimasuk.com/15842591/ brainstorm. (Accessed on 15 August 2019)
[10] A. Kengwinit, Application of experimental design for improving kurtosis process capability of pitch in suspension industry, Thesis, Chulalongkorn University, Thailand. 2010, pp. 7-16. (in Thai)
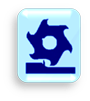