Reduction of Porosity in Investment-Casted Pink Silver: A Case Study of A Jewelry Company
DOI: 10.14416/j.ind.tech.2020.12.007
Keywords:
Investment Casting; Porosity; Pink Silver; Design of ExperimentsAbstract
Shrinkage porosity was a major defect found up to 56% in an investment-casted pink silver of the case study company. This research was aimed to reduce the defect by using experimental designs with full factorial design 3k strategy to study the influential casting factors and to find the optimal casting conditions. The casting factors included flask temperature and casting temperature while the response variable was the percentage of porosity area. Results showed that using the flask temperature at 600 oC with the casting temperature at 1030 oC or using the flask temperature at 480 oC with the casting temperature at 1060 oC provided the minimum percentage of shrinkage porosities. These optimal casting conditions reduced the percentage of defects by 29.5% on average.
References
[2] W. Mingvanich, Strategies to Increase Competitiveness in the Gem and Jewelry Industry, Department of Export Promotion, Ministry of Commerce, 2003. (in Thai).
[3] S. Yamkate, Export Problems with Gems and Jewelry of Thailand’s Gem and Jewelry Export Business, Independent Study, Rajamangala University of Technology Thanyaburi, Thailand. 2012. (in Thai).
[4] G.O. Verran, R.P.K. Mendes, and L.V.O.D. Valentina, DOE Applied to Optimization of Aluminum Alloy Die Castings, Journal of Materials Processing Technology, 2008, 200 (1–3), 120–125.
[5] F. Grosselle, G. Timelli, and F. Bonollo, DOE Applied to Microstructural and Mechanical Properties of Al-Si-Cu-Mg Casting Alloys for Automotive Applications, Materials Science and Engineering: A, 2010, 527(15), 3536–3545.
[6] J.K. Kittur, T.V. Herwadkar, and M.B. Parappagoudar, Modeling and Analysis of the Pressure Die Casting Using Response Surface Methodology, AIP Conference Proceedings, 2010, 1298, 735–741.
[7] U.A. Dabade and R.C. Bhedasgaonkar, Casting Defect Analysis Using Design of Experiments (DoE) and Computer Aided Casting Simulation Technique, Procedia CIRP, 2013, 7, 616–621,.
[8] G. Xuedan, L. Dunming, Z. Jianxin, and S. Xu, DOE Applied to Optimization of Steel Casting, Applied Mechanics and Materials, 2013, 251, 360–365,.
[9] J. Asensio-Lozano, J.F. Álvarez-Antolín, A. González-Pociño, and B. del Río-López, Optimization of Graphite Morphology in Mottled Nihard Cast Irons Inoculated with Feb and Manufactured by Centrifugal Casting, Metals, 2018, 8(5), 293.
[10] C.Q. Zheng and A. Simard, Optimization of Casting Parameters on an Improved AA6061 Aluminum Alloy for Semi-Solid Die Casting, SAE Technical Papers, 2010, 2010-01-0225, 1-12.
[11] S.M. Ali, The Effect of Reinforced SiC on the Mechanical Properties of the Fabricated Hypoeutectic Al-Si Alloy by Centrifugal Casting, Engineering Science and Technology, an International Journal, 2019, 22(4), 1125–1135.
[12] H. Hanizam, M. S. Salleh, M. Z. Omar, and A. B. Sulong, Optimisation of Mechanical Stir Casting Parameters for Fabrication of Carbon Nanotubes-Aluminium Alloy Composite Through Taguchi Method, Journal of Materials Research and Technology, 2019, 8(2), 2223–2231.
[13] M.P. Groover, Groover's Principles of Modern Manufacturing: Materials, Processes, and Systems, Global edition, John Wiley & Sons, Singapore, 2017.
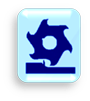