Improvement Work Method for Defect Reduction in Marking Brake Pad Process
DOI: 10.14416/j.ind.tech.2020.08.004
Keywords:
5W1H; ECRS Principle; Hypothesis Testing; Payback PeriodAbstract
Brake pad manufacturing found the incorrect position of text on brake pad defect in the marking process 10,976 pieces per day or 81% of the daily production plan and caused defects from 10 models. The temporary solution of the company before investigators studied process shown that provided an operator to arrange brake pad rows on the conveyor before pass the marking machine so caused to hire the operator. Investigators studied the work method by flow process chart, analyzed the value of activities, queried 5W1H shown that the main cause of the defect was inappropriate designing the conveyors in the process then applied ECRS principle to find improvement way by making new conveyors and adjusting the initial spacing of brake pad in the oven. The formula table was made by using 10 models to find the number of brake pads per row and appropriate initial spacing of brake pad to actual work. Result from statistical testing at 95% confidence level shown that adjusted the value of variables from formula table that could reduce the incorrect position of text on brake pad defect 10,976 pieces per day or 100% of the daily production plan. Besides, average capacity increased 1 piece per row and the payback period of improvement conveyors was 1.275 days.
References
[2] https://www.nairienroo.com/5w1h-to-ecrs/. (Accessed on 2 July 2020)
[3] https://greedisgoods.com/ecrs-%E0%B8%84%E0%B8%B7%E0%B8%AD/. (Accessed on 15 November 2019)
[4] P. Pattharathadakiat and D. Sutivong, Improvement of Standard Procedure in Beverage Concentrate Manufacturing Process, Engineering Journal of Research and Development, (2012), 23(1), 62-74. (in Thai)
[5] S. Klinmon, Production Efficiency Improvement in Lens Surface Grinding Process, Thesis, Industrial Engineering, Burapha University, Thailand. 2016.
(in Thai)
[6] T. Tussanarapun, Cost Reduction on Demineral Water Process: Case Study of Power and Steam Manufacturing Company, Thesis, Industrial Management Engineering, King Mongkut’s University of Technology North Bangkok, Thailand. 2008. (in Thai)
[7] P. Yaephuan, Engineering Economy, SE-EDUCATION Public Company Limited, Bangkok, 2003. (in Thai)
[8] T. Srisawangwong and N. Yodpijit, Work Improvement in an Automotive Parts Factory, Thai Industrial Engineering Network Journal, (2016), 2(3), 33-40. (in Thai)
[9] C. Taengpiw, Losses Reduction in Hot Roll
Coil Shearing Process, Thesis, Industrial Management Engineering, King Mongkut’s University of Technology North Bangkok, Thailand. 2011. (in Thai)
[10] https://sites.google.com/site/wichakarwicaythangkarsuksa/khea-su-bth-reiyn/hnwy-thi-8-sthiti-wicay-laea-kar-wikheraah-khxmul-1/khan-txn-ni-kar-thdsxb-smmtithan. (Accessed on 2 July 2020)
[11] A. Prasunjai and S. Vongpeng, Increase of Production Efficiency of Tractor Part by Industrial Engineering Technique: A Case Study of Automotive Part Factory, Pathumwan Academic Journal, (2020), 10(27), 55-69. (in Thai)
[12] https://www.scimath.org/lesson-physics/item/8781-2018-09-20-06-43-41. (Accessed on 15 November 2019)
[13] S. Suphap, Physics 1, SCIENCE PUBLISHING, Bangkok, 2018. (in Thai)
[14] http://www.stvc.ac.th/elearning/stat/csu10.html. (Accessed on 2 July 2020)
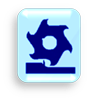