Effects of Peak Current and Nozzle Offset Distance on Wire Electrical Discharge Machining of Titanium
DOI: 10.14416/j.ind.tech.2020.03.007
Keywords:
Wire electrical discharge machine, Titanium, Material removal rate, Surface roughness, Kerf widthAbstract
The objective of this research was to study the effects of peak current and nozzle offset distance (NOD) as the arc gap on wire electrical discharge machining (WEDM) of titanium. Peak current was tested at three levels of 6, 7 and 8 A, while NOD was varied at 150, 175 and 200 mm. These three variables were assessed to achieve the highest material removal rate (MRR) that generated minimal surface roughness and kerf width. Results showed that a peak current of 8 A with NOD at 200 mm recorded the highest MRR of 0.57 mm3/min, while peak current at 6 A and NOD at 150 mm gave the lowest surface roughness at 2.02 µm and kerf width of 0.33 mm. A scanning electron microscope (SEM) was used to analyze the surface of the titanium. Findings determined that the lowest peak current (6A) and lowest NOD (150 mm) gave optimal surface roughness, MRR and surface cracks. Thus, these parameters can be used to improve the surface of titanium workpieces.
References
[2] T. Liu, J. Lin, Y. Guan, Z. Xie, L. Zhu and J. Zhai, Effects of Ultrasonic Vibration on the Compression of Pure Titanium, Ultrasonics, 2018, 89, 26 – 33.
[3] A.V.S. Prasad Ram, R. Koona and G.L. Datta, An Experimental Study of Wire EDM on Ti-6Al-4V Alloy”, Procedia Materials Science, 2014, 5, 2567 – 2576.
[4] S.P. Arikatla, K.T. Mannan and A. Krishnaiah, Parametric Optimization in Wire Electrical Discharge Machining of Titanium Alloy Using Response Surface Methodology, Materials Today: Proceedings, 2017, 4, 1434 – 1441.
[5] J. Kumar and J. S. Khamba, An Experimental Study on Ultrasonic Machining of Pure Titanium Using Designed Experiments, Journal of the Brazilian Society of Mechanical Sciences and Engineering, 2008, 30(3), 231 – 238.
[6] S.P. Arikatla, K.T.l Mannan and A. Krishnaiah, Surface Integrity Characteristics in Wire Electrical Discharge Machining of Titanium Alloy during Main cut and Trim cuts, Proceedings Materials Today: Proceedings, 2007, 4(2), 1500 – 1509.
[7] A. Kumar, V. Kumar and J. Kumar, An Investigation into Machining Characteristics of Commercially Pure Titanium (Grade-2) Using CNC WEDM, Applied Mechanics and Materials, 2012, 159. 56 – 68.
[8] A. Kumar, V. Kumar, J. Kumar, Surface Integrity and Material Transfer Investigation of Pure Titanium for Rough Cut Surface after Wire Electro Discharge Machining, Proceedings of the Institution of Mechanical Engineers, Part B: Journal of Engineering Manufacture, 2013, 228, 880 – 901.
[9] K. Ishfaq, N Ahmad, M. Jawad, M.A. Ali and A.M. Al-Ahmari, Evaluating Material's Interaction in Wire Electrical Discharge Machining of Stainless Steel (304) for Simultaneous Optimization of Conflicting Responses. Materials, 2019, 12(12), Article No. 1940, 1 – 15.
[10] D. De, T. Nandi and A. Bandyopadhyay, Analysis of Machining Parameters for Wire Cut Electrical Discharge Machining of Pure Titanium using Response Surface Methodology, Materials Today: Proceedings, 2018, 5, 2(1), 5374 – 5383.
[11] H.R. Tonday and A.M. Tigga, Analysis of Effects of Cutting Parameters of Wire Electrical Discharge Machining on Material Removal Rate and Surface Integrity, IOP Conference Series: Materials Science and Engineering, 2016, 115, 1 – 7.
[12] B.C. Khatri and P.P. Rathod, Investigations on The Performance of Concentric Flow Dry Wire Electric Discharge Machining (WEDM) for Thin Sheets of Titanium Alloy, The International Journal of Advanced Manufacturing Technology, 2017, 92, 1945 – 1954.
[13] A. Shah, N. A. Mufti, D. Rakwal and E. Bamberg, Material Removal Rate, Kerf, and Surface Roughness of Tungsten Carbide Machined with Wire Electrical Discharge Machining, Journal of Materials Engineering and Performance, 2010, 20, 71 – 76.
[14] T. Konishi, S. Habib, A. Okada, Y. Okamoto, and H. Kurihara, Influence of Nozzle Jet Flushing on Wire Deflection and Breakage, International Conference on Machining Materials and Mechanical Technology (IC3MT), 2014, 1 – 6.
[15] K. Takuro, A. Okada, Y. Okamoto and H. Kurihara, Effect of Tilting Jet Flushing Nozzle on Wire EDM Performance, International Journal of Electrical Machining, 2015, 20, 3 – 8.
[16] A. Okada, Y. Uno, S. Onoda, S. Habib, Computational Fluid Dynamics Analysis of Working Fluid flow and Debris Movement in Wire EDMed Kerf, CIRP Annals - Manufacturing Technology, 2009, 58 (1), 209 – 212.
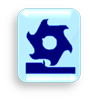