การศึกษาผลของแผ่นออริฟิซต่อระดับความรุนแรงของปรากฏการณ์คาวิเตชั่นภายในถังปฏิกรณ์แบบไฮโดรไดนามิกส์คาวิเตชั่น (The Study Effect of Orifice Plates on Intensifies Degree of Cavitation Phenomenon Inside Hydrodynamic Cavitation Reactor)
DOI: 10.14416/j.ind.tech.2020.03.006
Keywords:
Hydrodynamic cavitation reactor, Orifice plates, Cavitation numberAbstract
The objectives of this research were determined to optimize orifice plates for applying to use as a cavitation inducer device inside the hydrodynamic cavitation reactor. In this experiment, we focused on the comparison between five orifice plates with different configurations i.e., size, number, and shape of holds. The effect of different parameters such as operating condition (inlet pressure) and geometrical of the orifice plates (total perimeter holds, and
) have been studied. The experimental results showed that the inlet pressure considerably affects the degree of cavitation phenomenon when inlet pressure increases with decreasing cavitation number. Optimum inlet pressure of 4 bar gives a minimum value of cavitation number for all orifice plates. In addition, it was found that the geometry of the orifice plates plays an important role in the value of the cavitation number. The value of the cavitation number decreased with increasing parameter
and
. At the inlet pressure 4 bar, the results obtained confirmed that orifice plates OP-3 with the configuration of holes diameter was 2 mm and 24 holes performed better with cavitation number of 0.52 as compared to orifice plate OP-2, OP-1, OP-4, and OP-5, respectively when considered degree of cavitation phenomenon inside the reactor. In conclusion, the orifice plates OP-3 was more suitable for cavitation inducer devices in the hydrodynamics cavitation reactor for the biodiesel production process.
References
[2] P.R. Gogate, Cavitational Reactors for Process Intensification of Chemical Processing Applications: A Critical Review, Chemical Engineering and Processing: Process Intensification, 2008, 47, 515 – 527.
[3] P.R. Gogate and A.B. Pandit, A Review and Assessment of Hydrodynamic Cavitation as A Technology for The Future, Ultrasonics Sonochemistry, 2005, 12, 21 – 27.
[4] S. Manickam and A. Pandit, Wastewater Treatment: A Novel Energy Efficient Hydrodynamic Cavitational Technique, Ultrasonics Sonochemistry, 2002, 9(3), 123 -131.
[5] L.F. Chuah, S. Yusup, A.R. Abd Aziz, A. Bokhari, and M.Z. Abdullah, Cleaner Production of Methyl Ester Using Waste Cooking Oil Derived from Palm Olein Using A Hydrodynamic Cavitation Reactor, Journal of Cleaner Production, 2016, 112, 4505 – 4514.
[6] J. Carpenter, M. Badve, S. Rajoriya, S. George, V. Saharan, and A. Pandit, Hydrodynamic Cavitation: An Emerging Technology for The Intensification of Various Chemical and Physical Processes in A Chemical Process Industry, Reviews in Chemical Engineering, 2016, 33(5), 433 – 468.
[7] D. Ghayal, A.B. Pandit, and V.K. Rathod, Optimization of Biodiesel Production in a Hydrodynamic Cavitation Reactor Using Used Frying Oil, Ultrasonics Sonochemistry, 2013, 20, 322 – 328.
[8] G.L. Maddikeri, P.R. Gogate, and A.B. Pandit, Intensified Synthesis of Biodiesel Using Hydrodynamic Cavitation Reactors Based on The Interesterification of Waste Cooking Oil, Fuel, 2014, 137, 285 – 292.
[9] M.A. Kelkar, P.R. Gogate, and A.B. Pandit, Intensification of Esterification of Acids for Synthesis of Biodiesel Using Acoustic and Hydrodynamic Cavitation, Ultrasonics Sonochemistry, 2008, 15, 188 – 194.
[10] A. Pal, A. Verma, S.S. Kachhwaha, and S. Maji, Biodiesel Production Through Hydrodynamic Cavitation and Performance Testing, Renewable Energy, 2010, 35, 619 – 624.
[11] I. Worapun and N. Amattirat, Biodiesel Production from Waste Cooking Oil Using Hydrodynamic Cavitation Reactor, The Journal of Industrial Technology, 2019, 15(2), 55 – 69. (in Thai)
[12] I. Worapun, K. Pianthong, and P. Thaiyasuit, Influence of Orifice Plates on Percentage of Methyl Ester in Synthesis Biodiesel Process Under Hydrodynamic Cavitation Conditions, SWU Engineering Journal, 2014, 9(2), 1 – 11. (in Thai)
[13] L. Amin, P. Gogate, A. Burgess, and D. Bremner, Optimization of A Hydrodynamic Cavitation Reactor Using Salicylic Acid Dosimetry, Chemical Engineering Journal, 2010, 156, 165 – 169.
[14] J. Ozonek and K. Lenik, Effect of Different Design Features of The Reactor on Hydrodynamic Cavitation Process, Archives of Materials Science and Engineering, 2011, 52, 112 – 117.
[15] J. Carpenter, S. George, and V. K. Saharan, Low Pressure Hydrodynamic Cavitating Device for Producing Highly Stable Oil in Water Emulsion: Effect of Geometry and Cavitation Number, Chemical Engineering and Processing: Process Intensification, 2017, 116, 97 – 104.
[16] M. Bis, A. Montusiewicz, J. Ozonek, and S. Pasieczna-Patkowska, Application of Hydrodynamic Cavitation to Improve The Biodegradability of Mature Landfill Leachate, Ultrasonics Sonochemistry, 2015, 26, 378 – 387.
[17] L.F. Chuah, J.J. Klemeš, S. Yusup, A. Bokhari, and M. M. Akbar, A Review of Cleaner Intensification Technologies in Biodiesel Production, Journal of Cleaner Production, 2017, 146, 181 – 193.
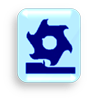